WHAT IS THE INDUSTRIAL METAL AGING PROCESS
Metal aging is a controlled heat treatment process used to increase the hardness, strength, and durability of certain alloys, particularly aluminum, titanium, copper, and some steels. This process takes advantage of changes in the microstructure of the metal, specifically through the precipitation of certain compounds, which increases the alloy's strength and durability.
Why is Metal Aged during the Manufacturing Process?
-
Increase Strength and Hardness
: The primary reason for aging metal is to increase its mechanical properties like hardness and tensile strength (the maximum stress that a material can withstand while being stretched or pulled before breaking), making it ideal for high-stress applications. -
Improved Wear Resistance
: Aging can enhance the wear resistance of metals, making them more durable in harsh environments thus increasing their longevity. -
Stabilizes the Microstructure
: The aging process helps create a more stable microstructure that resists further deformation under normal operating conditions. This stability is essential for metals used in structural and load-bearing applications.
Metals Most Commonly Subjected to Aging
-
Aluminum Alloys
: Aluminum alloys, particularly those in the 2000, 6000, and 7000 series, are commonly aged to improve strength, hardness, and corrosion resistance. The series numbers refer to the alloying element that has been added to the aluminum. 1000 Series is the purest aluminum—required to have 99% minimum aluminum. -
Titanium Alloys
: Titanium alloys used in aerospace and medical devices often undergo aging to enhance their mechanical properties like high strength, low weight, and resistance to corrosion. -
Copper Alloys
: Precipitation hardening in copper-based alloys increases hardness and conductivity. -
Precipitation Select Steels
: Some stainless steels (like martensitic and certain austenitic steels) are age-hardened to achieve higher strength.
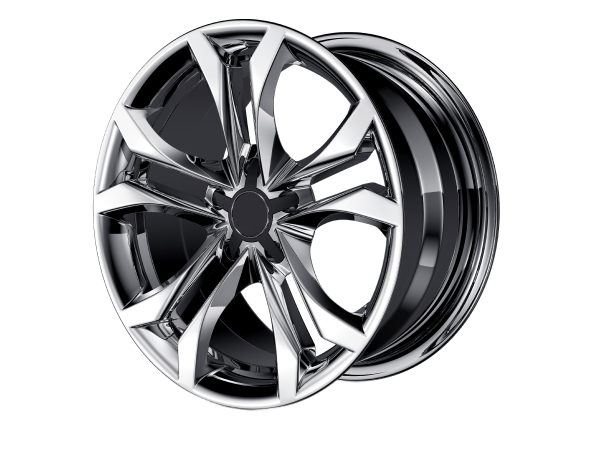
The Process of Metal Aging
The aging process typically involves the steps below, although times and temperatures will vary based on the metal type, part size, composition, and intended use. Horizon Industrial Ovens, equipped with Cyclone Technology™, excel in the rigorous demands of Solution Heat Treatment and Aging (Precipitation Hardening), setting a new benchmark for performance, precision, and efficiency.
-
Solution Heat Treatment
:- Objective: Dissolve alloying elements to create a homogeneous structure for aging aluminum, steel, and other alloys.
- Process: Horizon ovens ensure precise, uniform heating to the high temperatures needed (typically between 450°C to 550°C for aluminum alloys) without risk of localized overheating. Cyclone Technology™ optimizes heat distribution through powerful, multi-directional airflow. This controlled solution heat treatment guarantees the solute atoms dissolve uniformly within the metal matrix.
- Temperature: Typically, between 450°C to 550°C (for aluminum alloys).
- Cooling: With rapid cooling being critical to maintaining material properties, Horizon's advanced design integrates with quenching systems, ensuring minimal temperature variation across the part to "freeze" the solute atoms effectively.
Aging (Precipitation Hardening)
:- Objective: Precipitation hardening forces the solute atoms to form finely dispersed particles within the metal matrix, which hinder dislocation movement and increase strength.
- Process: After the solution heat treatment, the metal is reheated to lower temperatures (generally 100°C to 200°C for aluminum alloys). Cyclone Technology™ allows for superior temperature control and retention throughout this phase, resulting in consistent precipitate formation across the entire metal surface.
- Temperature: The aging temperature is typically lower than the solution heat treatment temperature, ranging from 100°C to 200°C for aluminum alloys, though it varies for other metals including copper, titanium, and precipitation-hardened steels.
- Cooling: Horizon's ovens maintain steady, controlled cooling post-aging, which is essential for precise metallurgical properties. With an ability to manage temperature holds for extended periods—from hours to days—Horizon ovens provide unmatched process reliability and repeatability.
Effects of the Aging Process on Metal Properties
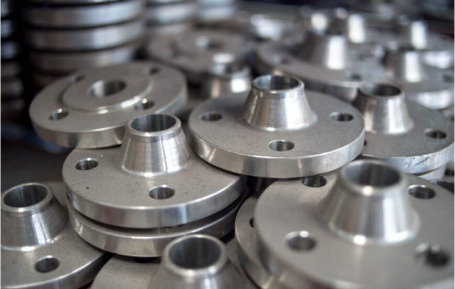
Applications of Aged Metals
-
Aerospace Industry
: Aging aluminum and titanium alloys used in aircraft structure and mechanics are frequently aged to meet the demanding strength-to-weight ratios for performance and durability. -
Medical Devices
: Titanium alloys used in implants like knees and hips are aged to provide the necessary mechanical properties and to make them biocompatible. -
Automotive Industry
: High-strength components undergo steel aging to provide durability in parts like automotive frames, engine parts, and suspension components. -
Industrial Tools
: Aging is used to strengthen cutting tools, dies, and molds, extending their service life and precision.
Ready to Optimize Your Manufacturing Process?
At Horizon, we're not just building industrial ovens; we're creating advanced thermal solutions that drive your business forward with cost-saving, eco-friendly technology. Contact us today to discuss your needs and discover how a custom Horizon Oven with Cyclone Technology™ can revolutionize your manufacturing process!