DRUM WASHERS
Rotary Drum Parts Washers have a rotating, perforated drum with an internal helix. The parts to be cleaned/processed are placed in one end of the drum, are tumbled and moved through the drum by means of the internal helix and the rotation of the drum, and the cleaned/processed parts exit the opposite side of the drum. Spray nozzles and piping are in the center of the drum, and spray water/solution onto the parts as they pass through the drum. Rotary Parts Washers can be single or multi-stage, and can also include drying or cooling of the parts.
Drum Washers are well suited to very economically clean a large volume of small parts such as stamped parts or fasteners. In addition to cleaning, they can also be used for a metal surface treatment process such as pickling or passivating. They are used in fabrication processes across many industries.
Rotary Drum Parts Washers can be batch or continuously fed. The parts are sprayed in each stage of the washer as they tumble and pass through the rotating drum. The drum is rotated by an electric motor driven chain or direct drive. Drum rotation speed is variable via VFD control. Each stage has its own stainless-steel tank and pump to spray water/solution onto the parts. The parts can also be immersed in sections of the washer by having a solid instead of perforated drum section. The solution/water of each stage may be ambient or heated by means of a submerged tube natural gas/propane burner or electric heating elements. Ambient or heated air drying is available. Ambient or chilled air cooling is also available.
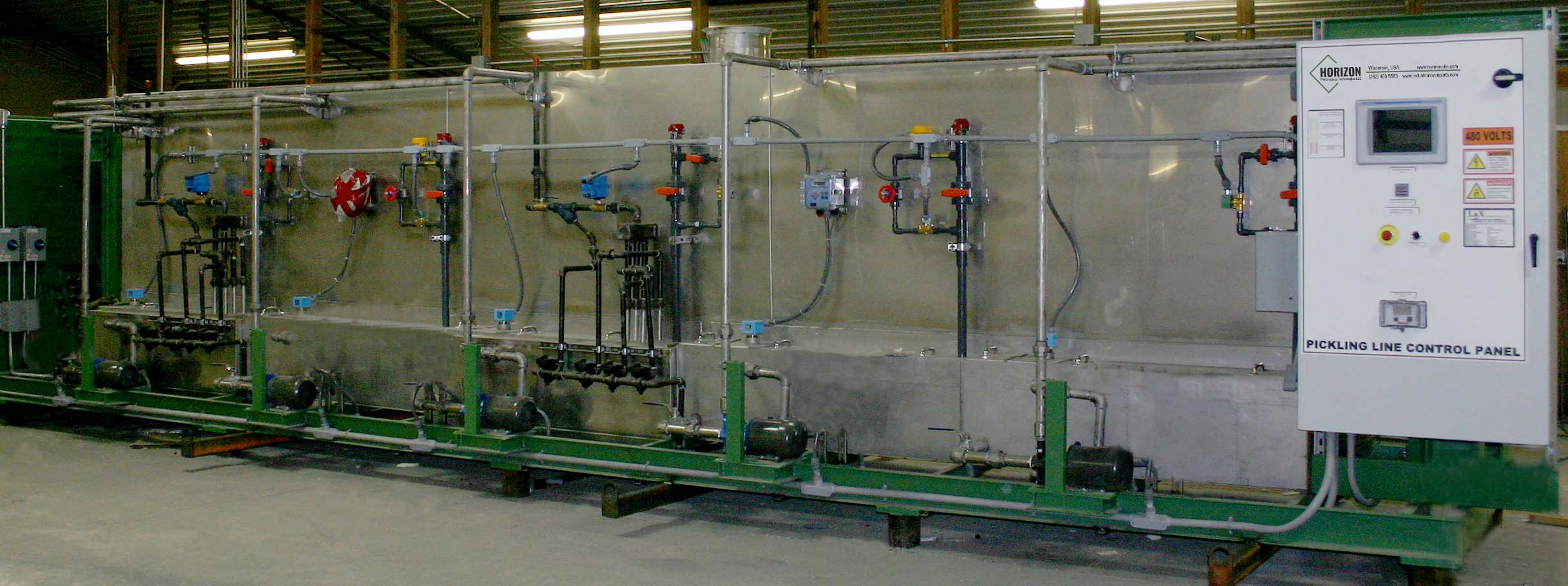
Efficiency and Innovation for Drum Washers
Horizon Performance Technologies LLC (Horizon) custom designs its Rotary Drum Washers for optimum performance and efficiency for the customer’s application. Product throughput required, product type and shape, required processes, number and types of stages, spraying or immersion, drum diameter, drum rotation speed, internal helix height/length/pitch, product cooling, product drying are just some of the factors considered by Horizon to produce the optimum design for the application.
Industrial Drum Washers feature a stainless-steel drum and internal helix, canopy, tanks, and process piping. The PLC with HMI enables control of drum rotation speed, flow rate and nozzle pressure for each stage, and specific recipes for various part types.
Horizon’s experience, and attention to detail and quality throughout all phases of the project, i.e., design, fabrication, installation, start-up, and post-installation follow-up, ensure the highest quality equipment and results.

- Stainless Steel construction – drum, internal helix, walls, roof, drain boards, and tanks.
- Stainless Steel piping.
- Stainless Steel, VFD controlled Pumps.
- Stainless Steel or clip-on polypropylene Nozzles.
- Stainless Steel, welded, leak tested tanks.
- Handles and latches off the tank covers are stainless-steel.
- Access doors.
- Screens in each tank located in the charge box areas, prior to the pumps.
- Optional electronic liquid level sensing and control.
- PLC with PanelView HMI.
- Maxon, Eclipse, or Midco natural gas or propane fired burners.
- Incoloy sheathed, electric, immersion heaters.
Industrial Drum Washer Construction and Features
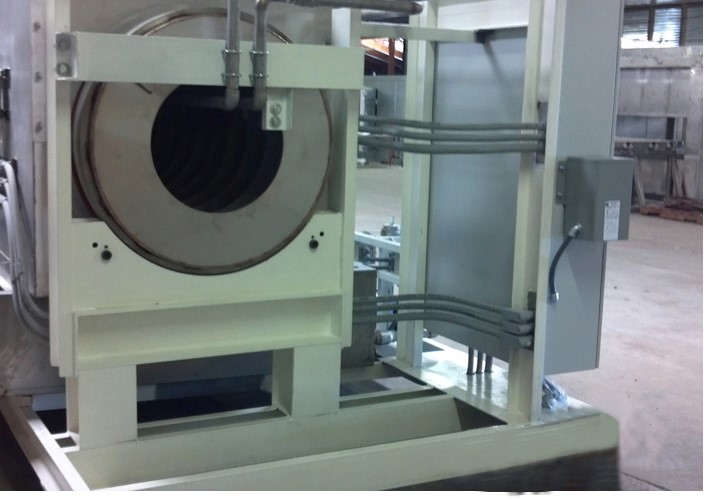
Industrial Drum Washer Accessories
Filtering – Unfiltered liquid enters the filter above the bag or basket and passes down through them where solids are contained. The covers of the filter are easily removable without tools.
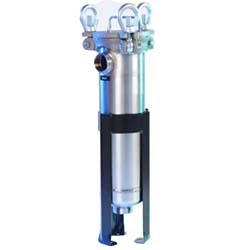
Magnetic Filter – Magnetic fines from the process water will be eliminated with the use of a magnetic filter/separator. Fines are collected where the water passes across the filter. The fines are easily removable because the filter is removable.
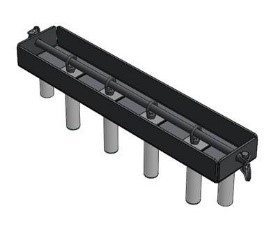
Oil Coalescer – Before the water returns to the tank the solution will be filtered and then will pass through oil separation. The tank is made up of 304 stainless steel and is welded water tight.
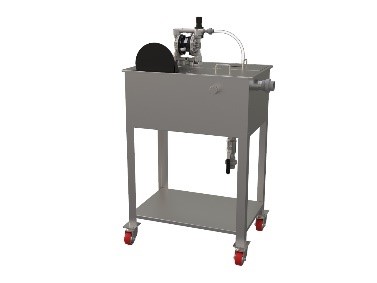
Blow-Off/Drying System –Air knives or air cannons are used to remove excess moisture from the products as they exit the washer. The air knives/cannons can be positioned to address areas where water tends to collect on the product. Compared to using compressed air, the blow off system is more efficient. Heated air blow-off is available.
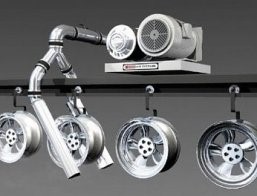
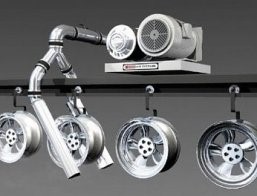
Mist Eliminator – If the rotary drum washer is being used for a metal surface treatment process such as pickling, preventing or reducing aerosolized pickling solution from being exhausted is desirable. The mist eliminator is a low pressure drop, vane type, with stainless steel construction, for vertical gas flow. It traps and drains a significant portion of the aerosolized coating liquid.
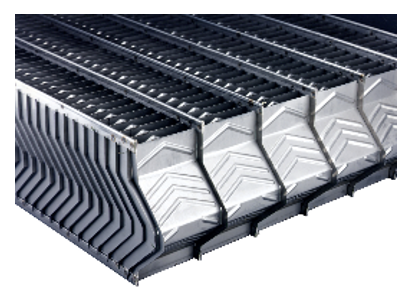
Water Treatment System – Reverse Osmosis (RO) is used in our water treatment system. Using RO can reduce water consumption, decrease chemical usage, and improve finish quality.
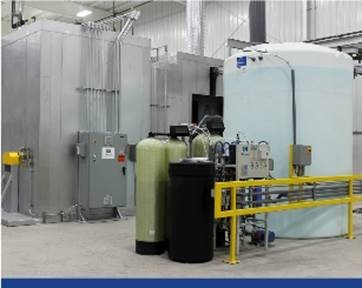
Brands
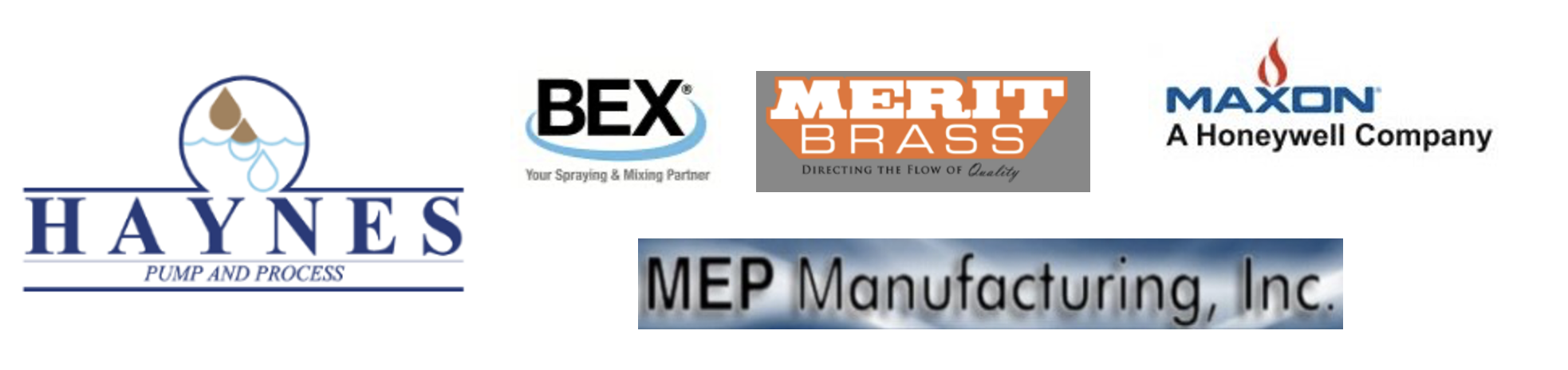