INDUSTRIAL OVENS WITH CYCLONE TECHNOLOGY™
PATENTED CYCLONE TECHNOLOGY™ FOR INDUSTRY LEADING EFFICIENCY
Horizon Performance Technologies LLC (Horizon) has developed its patented Cyclone Technology™ airflow design to provide steady temperature control all while significantly lowering utility costs up to 75%. This technology can be utilized in most standard or custom oven configurations from a basic single zone batch style oven to more complex multi-zone applications that may require a conveyor. Cyclone Technology™ (not to be confused with Cyclone Tech) features high volume airflow with low pressure.
The Cyclone Technology™ can be employed in applications with process temperature up to 1,200-degrees Fahrenheit. This technology can be applied to the following industries:
- Composites
- Heat Exchanger Process Equipment
- Paint
- Foundry
- Heat Treating
- Fastener
- Some Food Applications
- Automotive
- Aerospace
- Battery
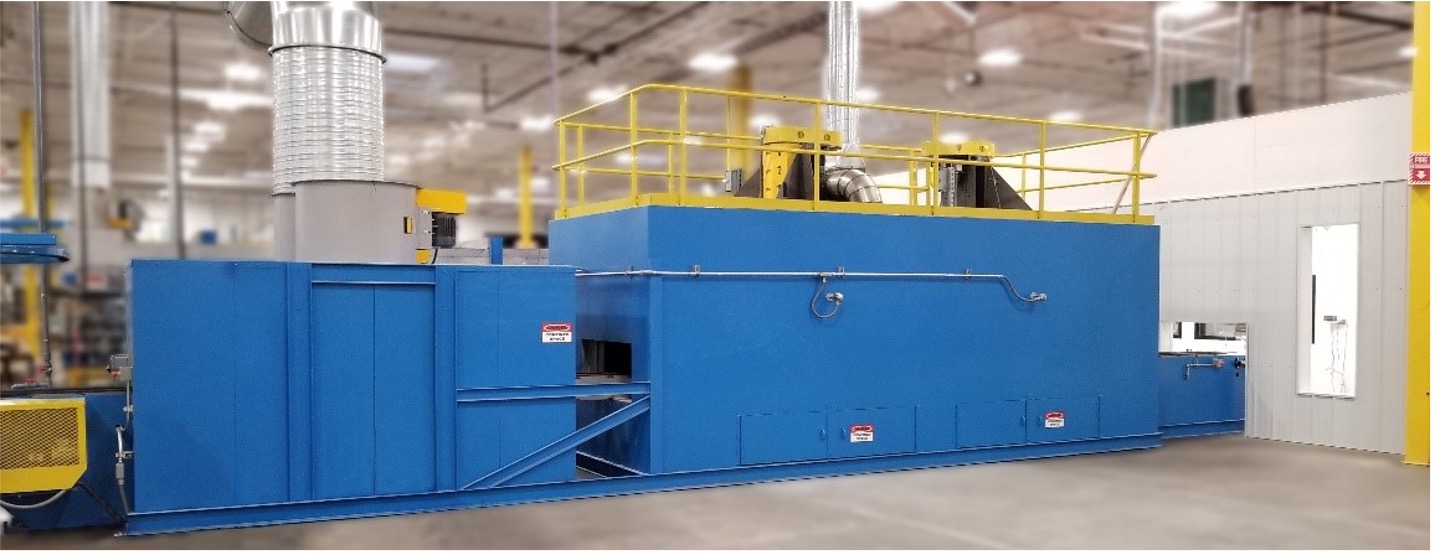
- Drying
- Curing
- Baking
- Annealing tempering stress relieving
- Aging
- Core wash
- Composite curing
- Pre-Heat
- Bonding
- Hydrogen embrittlement
- Web drying or curing
The unique Cyclone air flow is a superior option for most thermal heating processes:
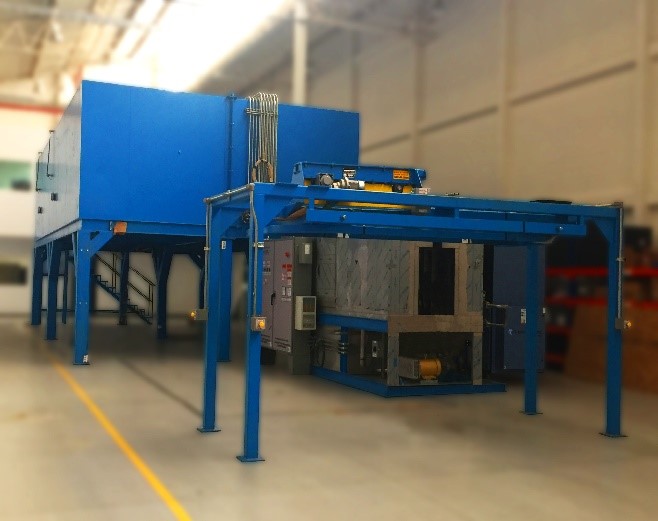
Efficiency and Innovation for Cyclone Technology™
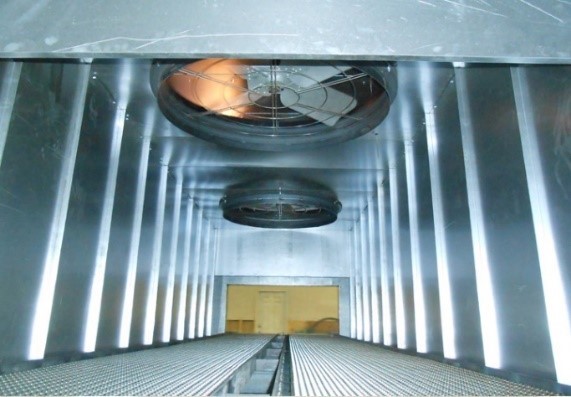
Cyclone Technology™ is a solution for maximizing floor space. Horizon’s technology improves heat transfer to the part, resulting in shorter process times. Shorter process times leads to shorter ovens, reducing overall foot print of the equipment.
Horizon constructs the interior of a Cyclone Oven™ with 18-gauge (GA) aluminized or stainless-steel sheet metal. Traditional ovens are typically designed with 20 GA aluminized or stainless-steel panels. The interior is eleven percent thicker than traditional ovens and acts as a radiant heat shield that is then reflected to the part. This provides a quality finished part at low cost all while enhancing temperature uniformity.
The Cyclone Technology™ also reduces electricity usage. A traditional oven uses large supply ductwork to move hot air to a part through nozzles. This requires an immense amount of horsepower (HP) on fan motors. Cyclone Technology™ emits air directly from a recirculation fan into the oven interior. The air then enters the return ductwork and travels through the burner flame and back to the recirculation fan. Convection heating is obtained once the air travels back into the oven interior. The fan motor HP on a Cyclone Oven™ is 1/5 to 1/4 the size of a traditional oven.
For example, a traditional oven fan running at 18,000 cubic feet per minute (CFM) will require approximately 2 ½ inch to 3 inch of static pressure enabling 4,000 feet per minute (FPM) at each individual nozzle. This requires a motor with 20-25HP. To attain the same 18,000 CFM, the cyclone fan will require only ¾ inch to 1 inch of static pressure. This requires only a 5 Hp motor. This is a savings of 75-80% in HP and ultimately kilowatts resulting in substantial operating savings each year over the ovens lifetime.
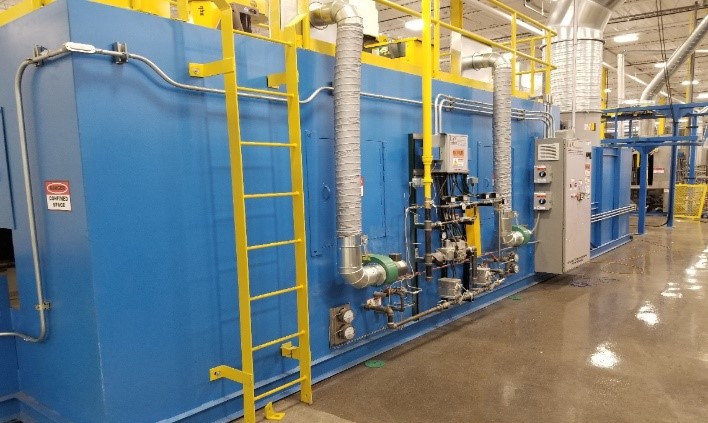
- Higher velocity at the part will transmit the heat into the product faster.
- Providing a swifter heat up time.
- Resulting in a more compact oven.
Performance of Cyclone Technology™
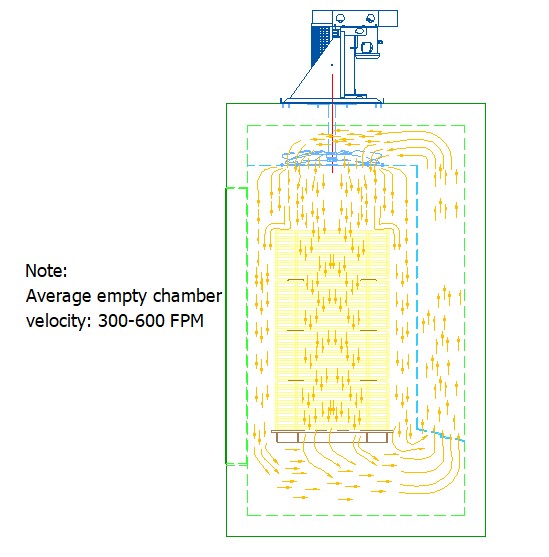
Temperature uniformity is a crucial part in the heating process of a part. Volume of airflow is the largest factor in achieving temperature uniformity. The more airflow moving and changing inside an oven, the better temperature uniformity. There is only so much air you can provide in a traditional oven when it is being pushed through nozzles at 4,000 FPM. Once the air leaves the nozzles, the velocity drops off very quickly. If 3/8” nozzles are spaced on 12” centers the air velocity will decline to 125 FPM on average through the part. The Cyclone Oven™ design does not contain supply nozzles at high velocities, which allows us to provide more total air compared to a traditional oven. All while doing it with less energy usage consumption.
The other benefit to having more air, is that the average velocity of the air running past the part is three to six times higher than traditional oven designs.
The curve images below visually show thermocouples attached to a part inside an oven:
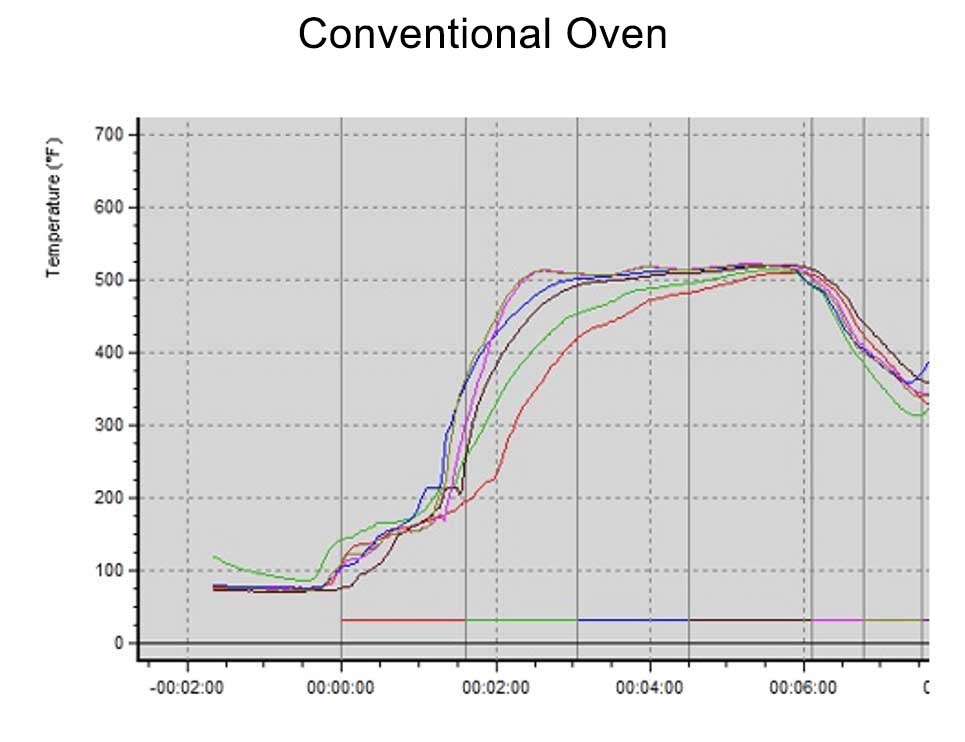
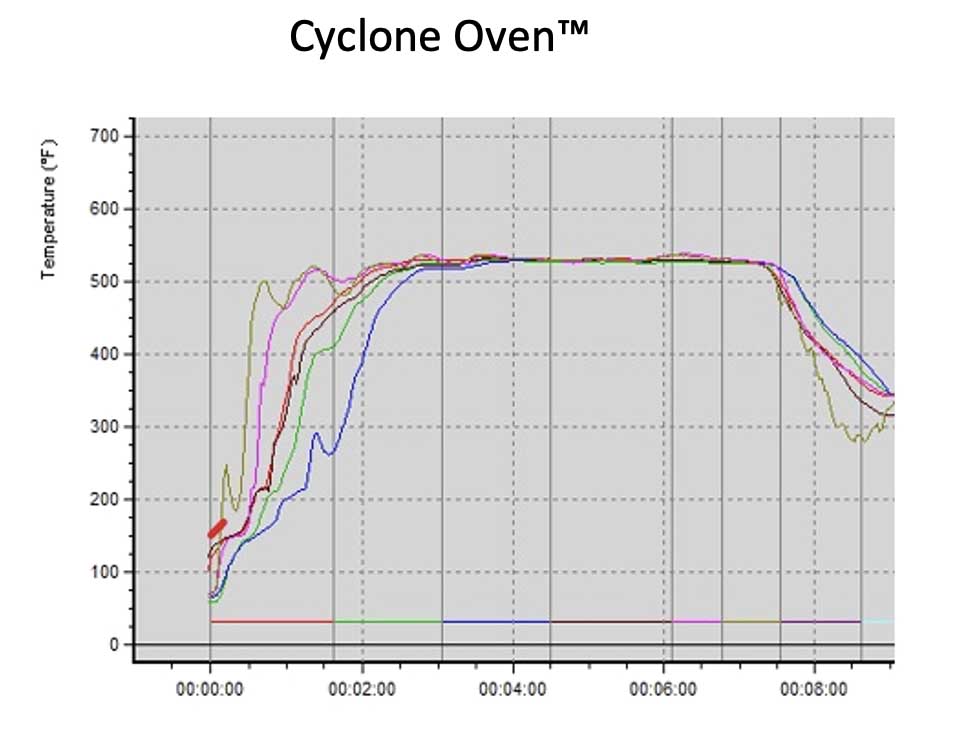
- Exterior construction of the oven is 3/16” plate and welded solid tight causing no heat losses.
- The Exterior construction design meets NFPA guidelines for oven design and fulfills the explosion proof criteria.
- Industrial grade Rockwell non-settling insulation is used with thickness ranging from three to six-inch for operating temperatures up to 1200 ⁰F (649 ⁰C).
- The interior shell is constructed of 18 gauge aluminized or stainless-steel.
- The internal return ductwork is constructed of 18 gauge aluminized or stainless-steel and brings recirculation air through the burner flame and back to the air recirculation fan into the oven interior. Additionally, the ductwork acts as a radiant heat shield that reflects heat to the parts surface.
- No extra support is needed for operators to walk on the roof of the oven due to robust construction.
- Equipped with maintenance doors to access the interior.
- Eclipse, Maxon or Midco propane or natural gas fire burners.
- Electric tubular heating elements.
- Maintenance plugs are used to access burners or heaters from floor level.
- Can be used for batch or multiple zones.
- Custom gas trains are available for gas-heated ovens.
- Variable frequency drives (VFD) are used on all fans and are controlled by using either a PLC with PanelView human machine interface (HMI) or VFD HMI’s.
The curve for the Cyclone Oven™ shows quicker heat-up time. It also shows the temperature uniformity is +/- five degrees Fahrenheit as compared to a traditional oven where the standard temperature uniformity is +/- ten degrees Fahrenheit.
Horizon Performance Technologies Cyclone Oven™ Laboratory
Horizon will perform an in-depth analysis of a customer’s part in our laboratory to meet or exceed the desired specifications. Horizon thermal engineers will evaluate the best possible solutions for heat processing of the part. A theoretical model test will be conducted in a full-scale industrial Cyclone Oven™. Technicians will data log the thermal performance of the part under varying scenarios. Indexing, continuous flow, batch processing, temperature settings and airflow affect the parts thermal performance. Thorough product testing and temperature recording using a Datapak, Horizon will create a full thermal profile.
Subsequent data analysis then provides the basis for the type of thermal processing system that is optimal for the customer and their part performance needs. This process of part testing ensures that the subsequent custom designed oven exceeds the customers expectation and ensures that the product performs predictably.
Cyclone Oven™ Construction and Features
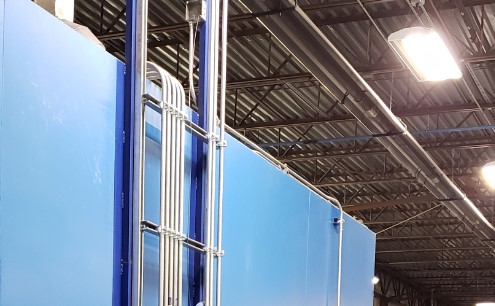
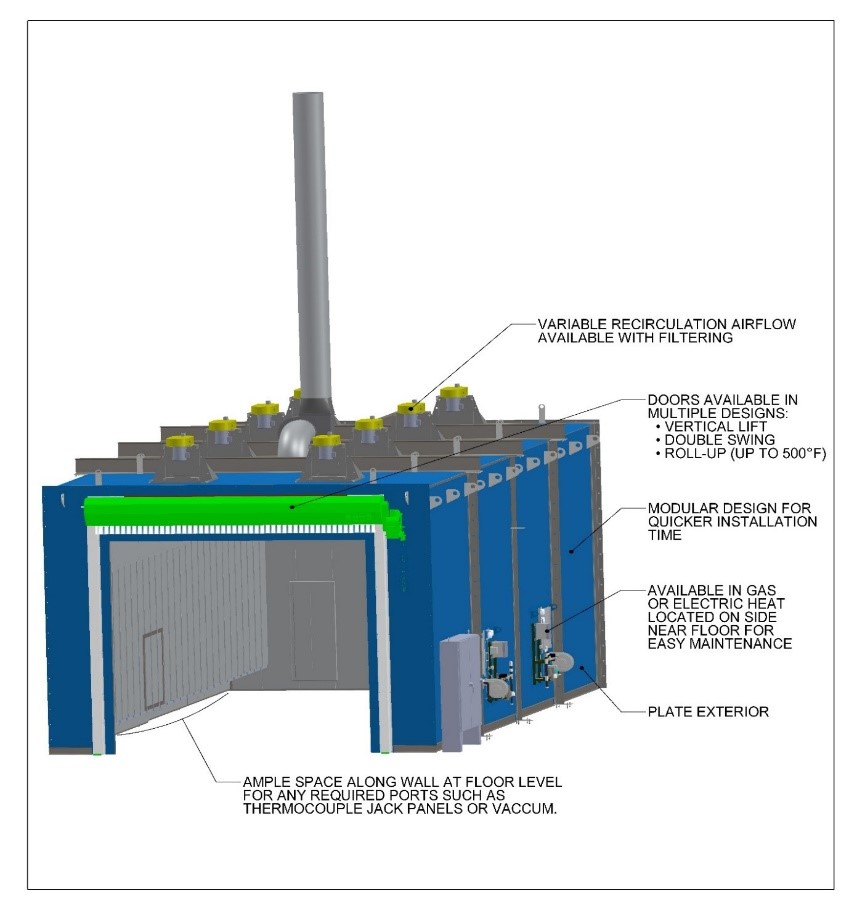
- Thermal Oxidizer
- Thermal Oxidizer with Heat Recovery
- Roof Safety Railings
- PLC Controls
- Vertical lift doors
- Roll-up Doors under 500 degrees F
- Access Ladders
Cyclone Industrial Oven Accessories
Brands
Below are some of the brands that we use for our Cyclone Technology™ Ovens.
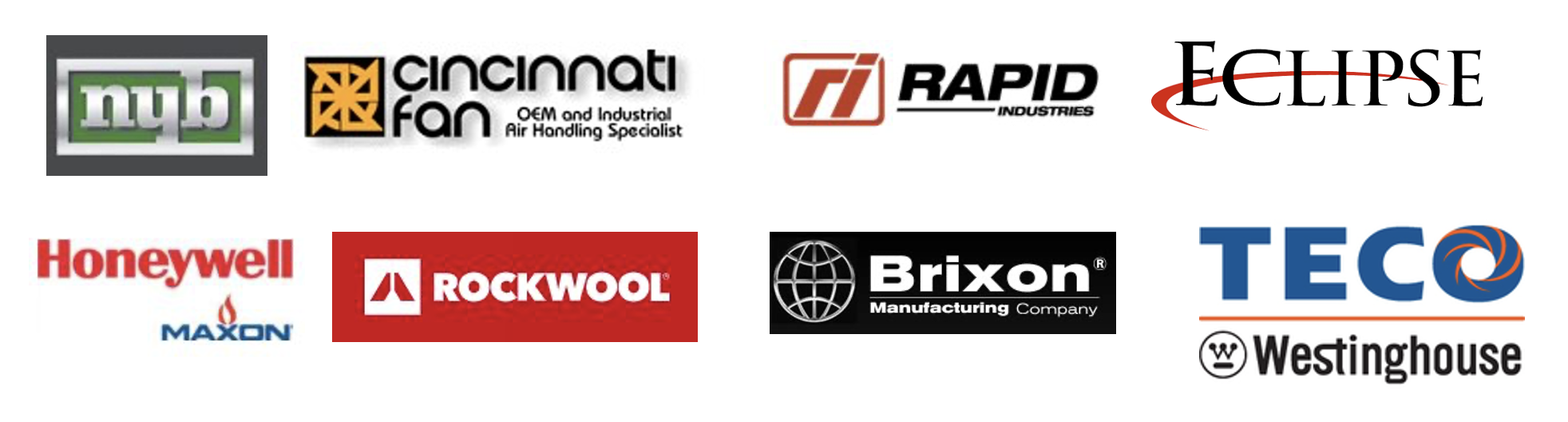