Industrial Batch Ovens
Industrial batch ovens are a type of thermal processing equipment widely used in the manufacturing and finishing processes of goods across various industries. Horizon Performance Technologies' batch type ovens are engineered for applications such as curing, drying, annealing, heat treating, and more. Designed as five-sided chambers with thermal insulation (often featuring high temperature concrete flooring) and a product access door. The size of the batch oven is determined by the largest substrate or part that needs to be processed. They excel at handling large parts, long heating durations, and low production flow scenarios, making them versatile tools in industrial and laboratory settings.
As a leading industrial oven manufacturer, Horizon Performance Technologies specializes in designing and building batch ovens that meet the most demanding production needs. Horizon manufactures both standard configurations and fully customized batch ovens. Our team of expert engineers works closely with you to ensure your oven is designed to meet the exact specifications of your production process.
Explore the applications and industries that benefit from our batch ovens below, and when you're ready to enhance your manufacturing efficiency, Contact Us today for a custom quote.

Industrial Batch Process Ovens Provide a Variety of Heating Solutions
- Adhesive/Gel Curing
- Composite Curing
- Quenching
- Aging
- Drying Water/Other
- Sintering
- Annealing
- Hardening
- Stress Relieving
- Burn Off
- Powder Coating
- Tempering
- Bonding
- Pre-heating
- Thermoforming
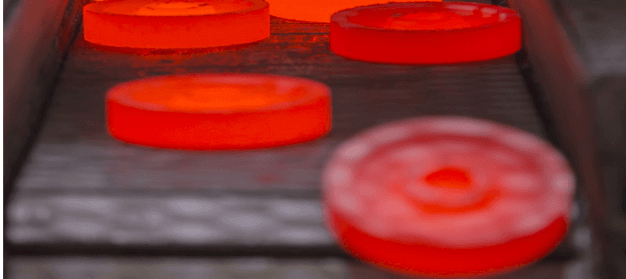
horizon Batch ovens serve a Wide Range of industries
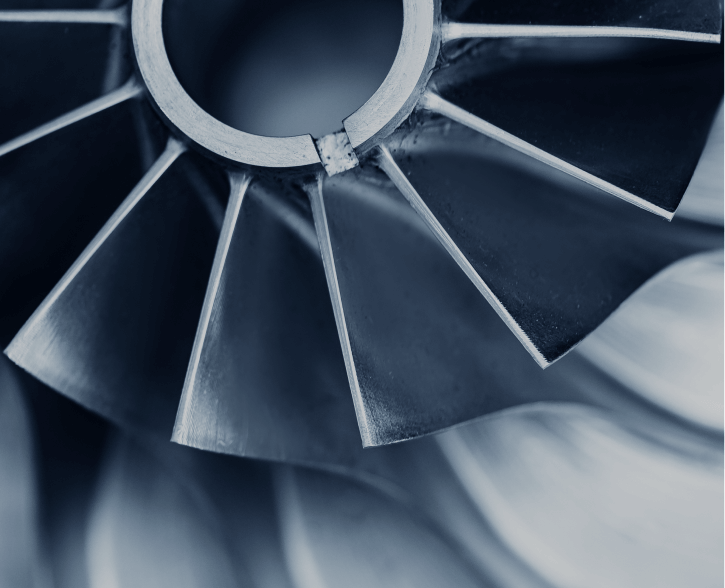
-
Aerospace:
Composite curing and high-temperature processes -
Automotive:
Curing automotive paints and heat treating metal parts -
Aluminum & Metal Fabrication:
Annealing, bonding, and finishing -
Battery & Energy:
Thermal processing of battery components -
Carbon Fiber & 3D Printing:
Post-processing and curing -
Electronics:
Drying and curing components -
Foundry:
Sand core drying and other high-temperature processes -
Healthcare:
Sterilizing and curing medical devices

Efficiency through Innovation: cyclone Technology™ saves money & resources
Horizon’s Cyclone Technology™ revolutionizes the efficiency of the industrial batch oven. By optimizing airflow and temperature distribution, it significantly reduces processing times and energy consumption. Cyclone Technology™ delivers up to 80% energy savings, significantly lowering operating costs while supporting sustainability goals by reducing your facility’s carbon footprint.
Key Benefits Include:
-
High-Efficiency Airflow:
High-volume, low-pressure airflow to optimize heat transfer, leading to shorter process times. -
Reduced Motor Horsepower:
Cyclone Ovens™ require 75-80% less motor horsepower for recirculation fans compared to conventional ovens, resulting in substantial electricity savings over the equipment's lifetime. -
Energy Conservation and Savings:
Increased insulation thickness minimizes gas consumption, lowers BTUs needed for heating, and reduces wall loss (the heat energy that escapes through the walls of the oven, rather than being retained within the oven chamber), leading to significantly lower operating costs. -
Smart Control Systems:
Equipped with variable frequency drives and HMI systems, Horizon's batch ovens offer precise control over the heating process, ensuring consistent temperature control and adaptability to changing production loads. -
Reversible Air Recirculation:
Automated through PLC controls, this feature allows the oven to reverse airflow during cycles, ensuring uniform heat distribution and enhancing process capabilities for sensitive materials.

superior Performance: The Cyclone Technology™ difference
-
Temperature Uniformity:
Cyclone Technology™ provides the industry’s most superior temperature uniformity allowing for a more consistent product temperature. This ensures the highest possible product quality, and is especially critical in industries like aerospace, automotive, and composites manufacturing. -
Faster Heat-Up Times:
Higher velocity airflow at the product surface enables quicker heat transfer, resulting in shorter heat-up times. In some cases, this may allow for the use of smaller batch ovens (depends on the specific requirements of each application). -
Motor Size Versus Conventional Ovens:
Unlike conventional ovens that rely on high-velocity nozzles which lose efficiency quickly, Cyclone Technology™ maintains consistent airflow and temperature with motors that are 1/4 to 1/5 the size, delivering better performance with less energy. -
Versatility Across Applications:
Our custom batch ovens produce high quality results in a variety of processes and industries. Whatever your challenge, Horizon can custom engineer and build the exact oven you need!
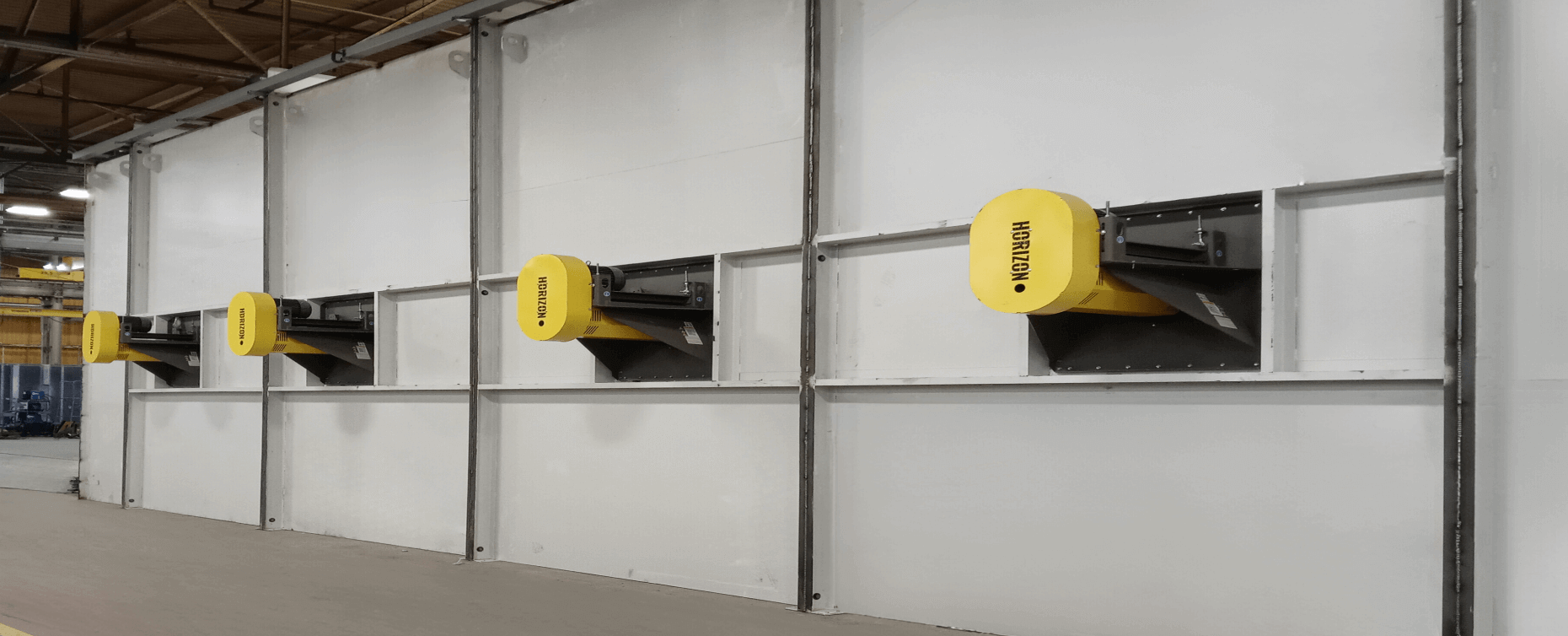
robust construction: Built for exellence-built to last
-
Durable Exterior Construction:
Horizon’s batch ovens feature a solid plate construction that is 500% thicker than conventional panel designs, preventing heat loss and contamination. The design meets NFPA guidelines and is explosion-proof. -
Seamless Design:
The welded-tight construction eliminates seams that could leak heat or allow contaminants to escape, maintaining a clean exterior and efficient heat retention within the oven. -
Superior Insulation:
The non-settling rockwool insulation, with wall thicknesses ranging from 4 to 8 inches, ensures optimal performance at temperatures up to 1200°F. -
Enhanced Interior Features:
The oven's interior is crafted from aluminized or stainless steel that is 25% thicker than typical industrial ovens. The design minimizes exterior support structure, reduces thermal bridges, and enhances heat reflection for better product processing. -
Modular Design for Future Expansion:
Ovens can be designed so that the modular construction enables easy future expansion, adapting to growing production demands without the need for a complete oven overhaul. -
Customizable Options:
Horizon offers various accessories, including roof safety railings, access ladders, PLC controls, roll-up doors (under 500°F), thermal oxidizers, and heat recovery systems, allowing for tailored solutions to specific industrial needs.
Not sure which industrial oven is right for your process?
Horizon offers a full line of industrial ovens engineered for precision and performance, including but not limited to:
-
Conveyor Ovens
for high-volume, continuous production lines. -
Walk-in / Truck-in Ovens
for oversized parts and bulk material handling. -
Dip-Spin Ovens
for post-coating curing in dip-spin systems (both batch & conveyor style). -
Vacuum-ready Composite Curing Ovens
(OOA) for curing of composites using vacuum bagging especially suited for aerospace, automotive, and sporting goods applications.
Ready to Optimize Your Manufacturing Process?
At Horizon, we're not just building industrial batch ovens, we're creating solutions that drive your business forward in a cost-saving, eco-friendly way. Contact us today to discuss your needs and discover how a custom Horizon Oven with Cyclone Technology™ can revolutionize your manufacturing process!