A cabinet or batch washer is used to pretreat metal parts prior to powder or liquid coating. The parts are brought into the washer in “batches” rather than moving through on a continuous conveyor. The parts are typically on carts or hung on a manual or indexing conveyor.
A cabinet washer can have one product door for parts to enter and exit, or an entry and exit door on opposite sides. Because the parts are “cleaned” in place, a cabinet or batch washer will have a smaller footprint, and a lower equipment cost, than a comparable continuous washer. Compared to manual cleaning in a wash booth, a cabinet washer will have a smaller footprint, which will reduce the exposure of personnel to chemicals, and is less labor intensive.
Horizon Performance Technologies LLC (Horizon) utilizes its Torrent Technology™ in its cabinet pretreatment washers. Pretreatment washers clean and prepare metal parts prior to the application of a coating. This is typically a multi-stage process that cleans and applies a conversion coating to the parts prior to powder or liquid coating. The pretreatment process improves the adhesion of the powder or liquid coating to the part surface and increases its effective longevity.
The cabinet or batch pretreatment washers have solution/water tanks for each stage of the multi-stage processes. The liquid in these tanks is pumped through spray nozzles onto the parts inside the canopy of the washer.
In a batch washer, the parts are stationary and each stage of the washer is applied to the parts in sequence. In Horizon Torrent Technology cabinet washers, the common process piping is blown out with compressed air between the operation of each stage, thereby reducing “carryover.”
Pretreatment washing processes are used by virtually every manufacturer that uses painted metal parts in their products; whether directly in their own in-house powder/paint line, or indirectly through out-sourcing. Cabinet washers with Horizon Torrent Technology™ are also used for single stage, pre-treatment, coating processes. An example of this would be an organic phosphating process, such as Plaforization.
Efficency & Innovation for Cabinet Washers

Horizon’s patented Torrent Technology™ cabinet washers have rotating riser bars with attached nozzles. The spray nozzles move in a circular pattern as the riser bars rotate. The circular rotation of the nozzles enables spray coverage of the parts with less nozzles, and thus less water flow. Less water flow means less pump horsepower and electrical energy costs, and less chemical usage. The rotating action of the risers result in a swirling spray pattern which provides excellent coverage, even in difficult to reach spots, and excellent cleaning results. The rotational velocity adds to the impingement of the water spray on the parts. The pumps and rotating motors are VFD controlled, enabling adjustable control of flow, pressure, and rotational speed.
The innovative, patented, Torrent Washer™ design, exclusively produced by Horizon supersedes the older conventional design of washers, which uses multiple riser columns of many stationary nozzles.
- Because of the rotating nozzle bars, the Torrent design enables a multi-stage pretreatment process in a single cabinet. The swirling spray pattern ensures excellent coverage of the parts, despite the parts being stationary inside of the washer cabinet. A multi-stage Torrent Cabinet Washer has a much smaller footprint compared to a continuous multi-stage washer, and a lower equipment cost.
- Compared to a manual wash booth, a Horizon Torrent cabinet washer will have a smaller footprint, less exposure of personnel to chemicals, and will require less labor to wash the parts.
- Greatly improved wash solution/rinse application resulting in better chemical application and/or part cleaning. The velocity of the spray application is greatly increased because of the rotation or sweep velocity of the rotating risers. This results in greatly increased chemical application and/or cleaning of complex surfaces of the work piece. A typical average nozzle rotational or sweep velocity is 70 ft./min.
- Lower wash solution/rinse flow resulting from replacement of the multiple riser columns in a typical washer design. Most washers with the Torrent design have 1/5 the number of spray nozzles of a standard riser type washer. This greatly decreases the operating cost of a washer because of the following:
- Reduced amount of energy needed to heat solution because of lower evaporation loss from the sprayed wash solution. This also means less water make-up, less chemical usage, and lower washer exhaust requirements. The lower exhaust requirements greatly reduce air make-up needs for the factory and results in lower energy needs for air make-up and air injection to the factory. Many Torrent Washers™ require no exhaust systems.
- Smaller pump sizes because of lower solution flow required. This results in lower pump energy use.
- Lower wash solution/rinse capacity is required. This results in smaller tanks, which result in lower disposal expense of spent solutions.
- Greatly reduced quantity of nozzles which means less maintenance is needed inside the washer.
The advantages of using Torrent Technology™ for Cabinet Washers include:
Batch Washer Performance
The rotating nozzle bars/arms create a swirling spray pattern which excels at cleaning the leading and trailing ends of the parts, as well as hard to reach pockets. The rotating action also adds rotational velocity which increases impingement and coverage.
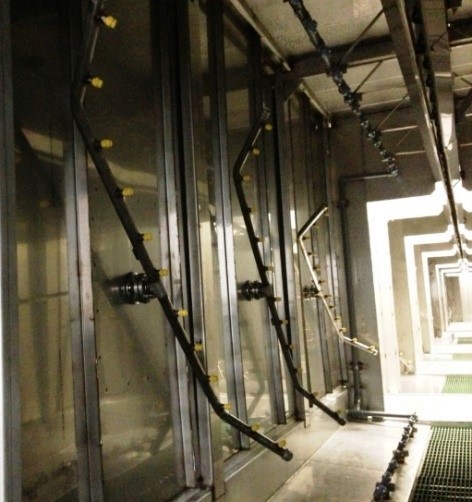
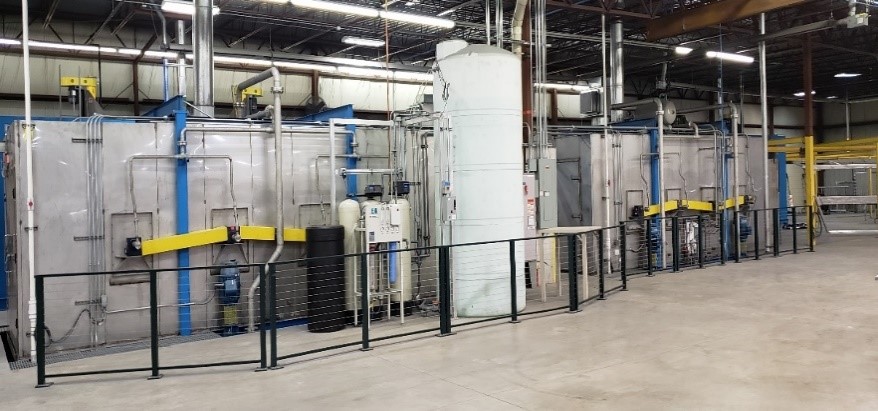
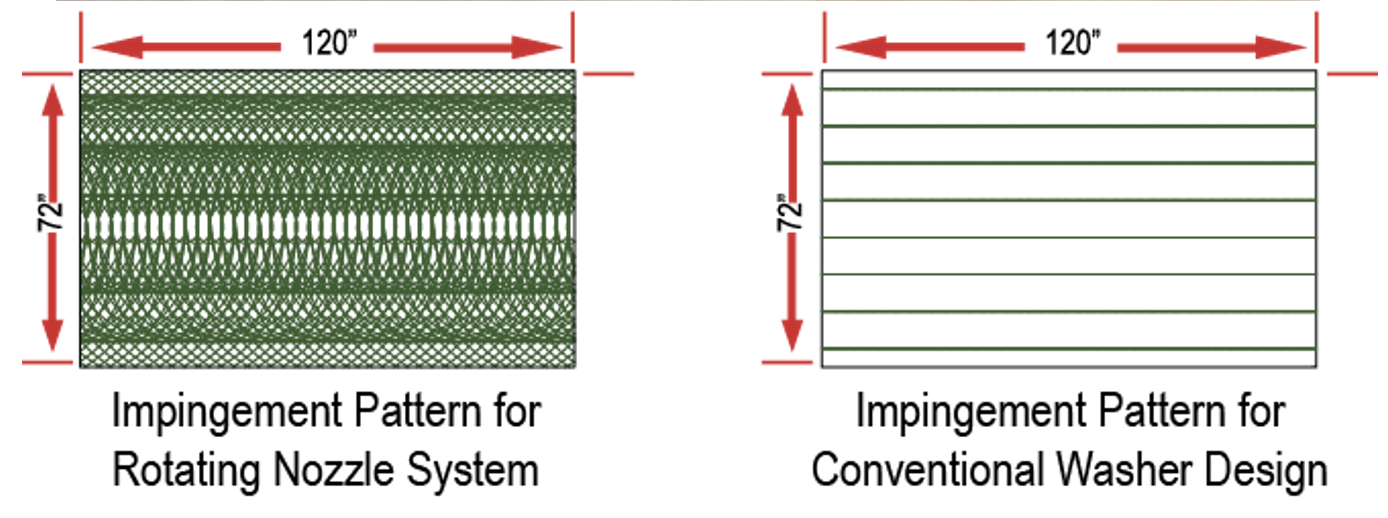
- Stainless Steel Construction – roof, walls, drain boards and production doors.
- Stainless Steel Wetted pumps.
- Stainless Steel Process piping.
- Stainless Steel Nozzles.
- Stainless Steel Plank grating for internal walkway.
- Stainless Steel, welded, leak tested tanks. Tank bottoms are pitched to a drain connection.
- Stainless Steel Tank covers with handles and latches.
- Vertical Pumps – seal less and VFD controlled.
- The rotating risers have adjustable speed drive mechanisms, which allows them to not be dependent on water pressure.
- The rotating unions are ceramic coated stainless steel, and oversized gearboxes are used for years of trouble-free service.
- Header pressure is continuously monitored.
- Access doors.
- Screens in each tank located in the charge box areas, prior to the pumps.
- Optional electronic liquid level sensing and control.
- Optional internal lights.
- PLC with PanelView HMI – allows adjustment of nozzle arm rotational speed, nozzle flow, and cycle times. Also, specific recipes can be developed and programmed, such as recipes for light, medium, and heavy parts.
- Maxon, Eclipse, or Midco natural gas or propane fired burners.
- Incoloy sheathed, electric, immersion heaters. Flanged connections for ease of maintenance.
- Compressed air tank to blow out common process piping between stages, decreasing “carryover.”
Batch & Cabinet Washer Construction and Accessories
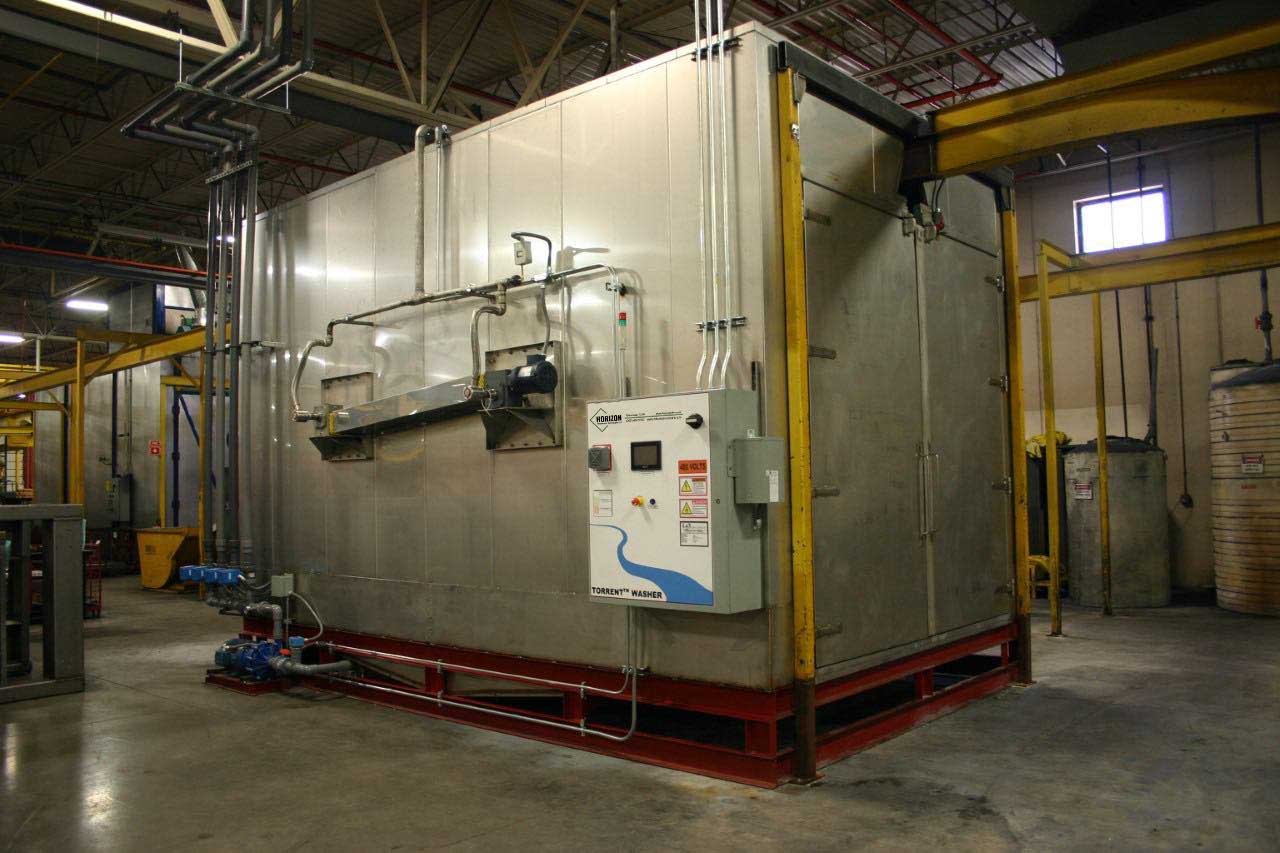
You can use this widget to input arbitrary HTML code into the page. Invalid HTML code may cause issues with the preview pane.
Batch & Cabinet Washer Accessories
Filtering – stainless steel bag filter housings equipped with isolation valves. Pressure monitoring is available which will provide for filter cleanliness and pressure feedback. This can notify the operator to maintain the filter and/or shut down the system if the filter is not changed and the system falls out of spec.
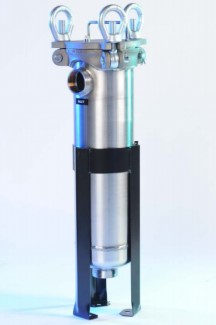
Magnetic Filter - Magnetic Separator with Drain Board to remove magnetic fines from the process water. The return water passes across the magnetic filter where fines are collected. This accessory is removable from the washer to allow for easy removal of the fines.
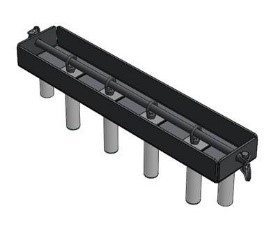
Internal LED Lighting – LED lights mounted externally to the chamber, over a tempered glass window. The operator can turn the lights on/off via the operator interface terminal.
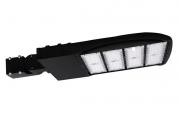
Oil Coalescer – The unit is located next to the washer and works in a side stream fashion, drawing a water/oil mixture off the top using a floating head and diaphragm pump. The fluid is routed through a filter bag and then through multi-matrix plastic coalescing media. The removed oil is routed to a container for disposal by the customer. The remainder of the fluid is returned to the washer. Coordination with the chemical vendor is recommended.
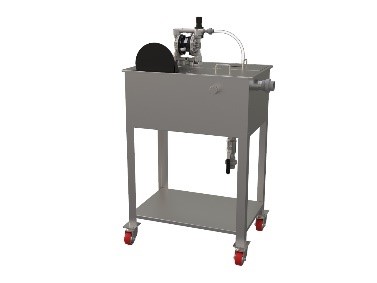
Blow-Off System – A high efficiency blower is used with air knives or air cannons to remove excess moisture from the products as they exit the washer. The adjustable air knives/cannons are located inside the canopy at the exit of the washer. The air knives/cannons can be positioned to address areas where water tends to collect on the product. The system is much more efficient than using compressed air for blow-off.
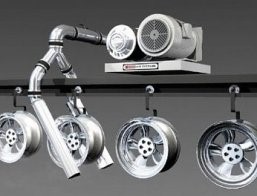
Mist Eliminator – If the Torrent Washer™/coater is being used for a coating process, such as an organic phosphating process like Plaforization, conserving the coating liquid is economically desirable. The mist eliminator is a low pressure drop, vane type, with stainless steel construction, for vertical gas flow. It traps and drains a significant portion of the aerosolized coating liquid that would otherwise be carried out with the exhaust.
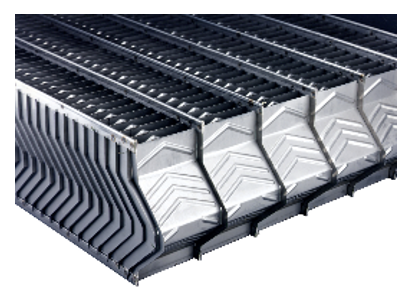
- Carbon filter, FRP tank, brass control valve, for chlorine removal from city water supply.
- Duplex water softener, FRP tanks, water meter, salt tank with salt grid and safety shutoff float, for removal of mineral hardness from the water supply.
- Reverse Osmosis machine to reduce the incoming water total dissolved solids by 97-98%. Includes: low energy membranes, permeate and concentrate flow meters, concentrate and recycle flow control valves, high pressure pump, 316 SS membrane housings, automatic inlet shutoff valve, low inlet pressure switch, inlet and outlet sample valves, pre filter – post filter – primary and final pressure gauges, 1.0 micron pre filter, powder coated steel frame, and NEMA 1 control box.
- Transfer pump to continuously circulate the stored RO water and pressurize the water going out to distribution.
- Poly RO water storage tank. Includes flow controller with internal piping to continuously circulate and mix the RO water.
- Conductivity meter and sensor for remote monitoring of the stored water quality.
- UV light in 316 SS housing installed in the RO storage tank recirculation line piping, for bacteria kill.
Water Treatment System - Complete Water Treatment Systems are available including:
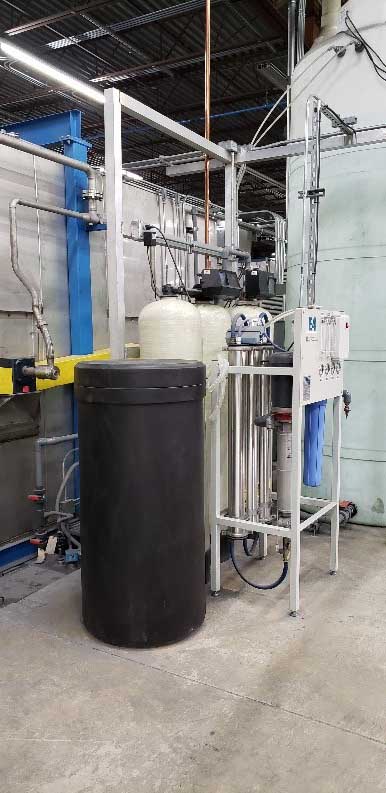
Brands
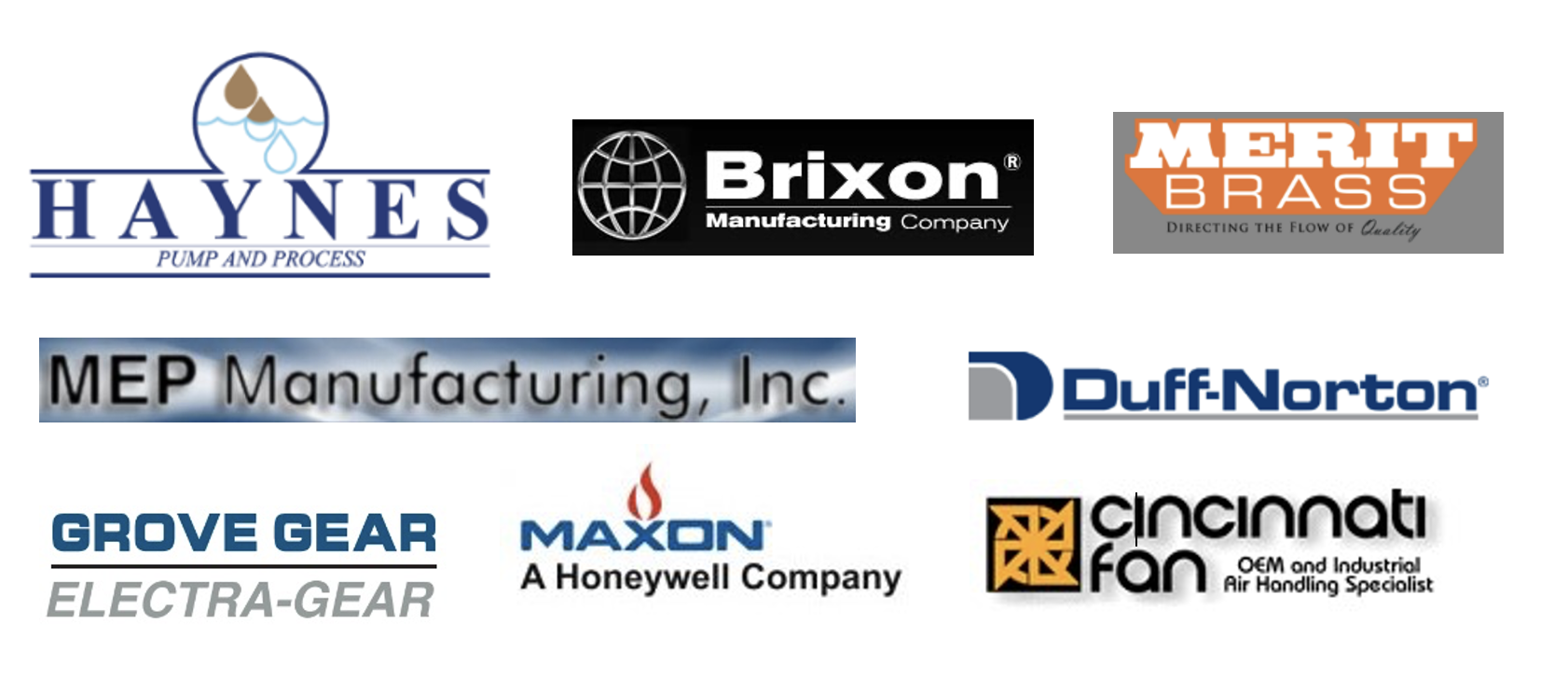