Conveyor Driven Belt Washers — also known as conveyor washers — are used to clean parts after a machining or manufacturing process, and/or to prepare parts for powder or liquid coating. The process can simply be a cleaning and rinse, or a multi-stage process that includes a conversion coating. Stages may be heated, and ambient or heated forced air drying may be included in the washer.
The parts move through the spray washer on a conveyor-driven belt. The belts are typically stainless-steel flat wire mesh, balanced weave, or formed wire. The belt can also be non-metallic. The belt type and width are chosen to best fit the application.
The parts are commonly manually loaded on the conveyor, placed in a basket or frame and onto the conveyor, or onto formed fixtures that are part of the belt. The parts can also be loaded onto the washer’s belt conveyor from another process conveyor, and unloaded onto a downstream conveyor.
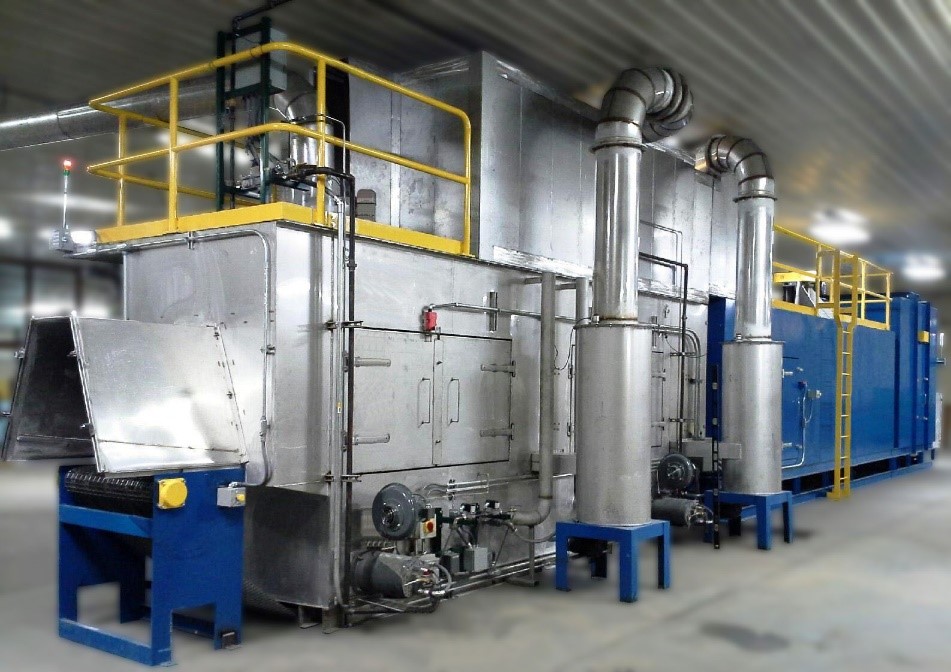
Conveyor Driven belt washers are suited for high throughput, for parts that are impractical to be hung on a conveyor, or small parts. The conveyor belt speed is adjustable via VFD control.
If the washer is used to clean and prepare metal parts prior to the application of a powder or liquid coating, typically a multi-stage process is employed. The parts are cleaned, and a conversion coating is applied to the parts prior to powder or liquid coating.
The pretreatment process improves the adhesion of the powder or liquid coating to the part surface and increases its effective longevity.
These multi-stage conveyor washing systems are ideal for facilities requiring continuous throughput and consistent quality on metal parts. The pretreatment washers have solution/water tanks for each stage of the multi-stage process. The liquid in these tanks is pumped through spray nozzles onto the parts inside the canopy of the washer. The parts move through each of the washer’s stages on the belt-driven conveyor.
Multi-stage pretreatment washers are used by virtually every manufacturer that uses metal parts in their products; whether directly in-house, or indirectly through out-sourcing.
Efficiency and Innovation for Belt Washers
Horizon Performance Technologies custom designs its conveyor belt washing systems to provide the optimum equipment for the customers’ products and processes. Product type and shape, required throughput, spray pattern requirement, type of belt, belt width, various spray application stages, any required drying, etc., are all factors considered in the design of the washer.
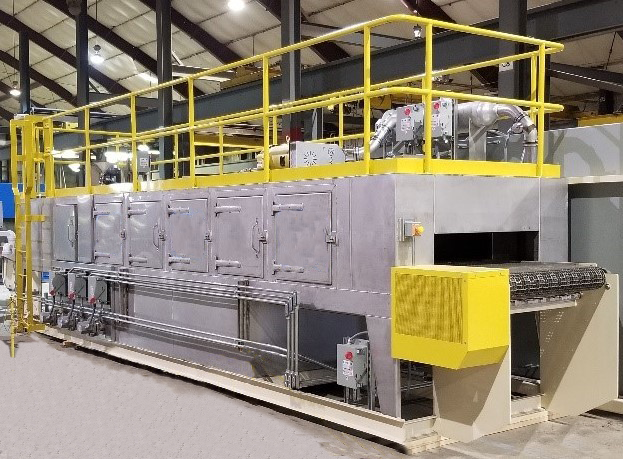
Each belt parts washer is built using durable materials and advanced control systems to ensure long-term, repeatable cleaning performance. The Conveyor Driven Belt Washers feature stainless steel construction and process piping. The PLC with HMI enables control of belt speed, flow rate and nozzle pressure for each stage, and specific recipes for various part types.
Horizon Performance Technologies attention to detail and quality throughout all phases of the project, i.e., design, fabrication, installation, start-up, and post-installation follow-up, ensure the highest quality equipment and results. Torrent Technology™ can be applied for some belt washer applications. For more information on Torrent, see our Torrent Technology™.
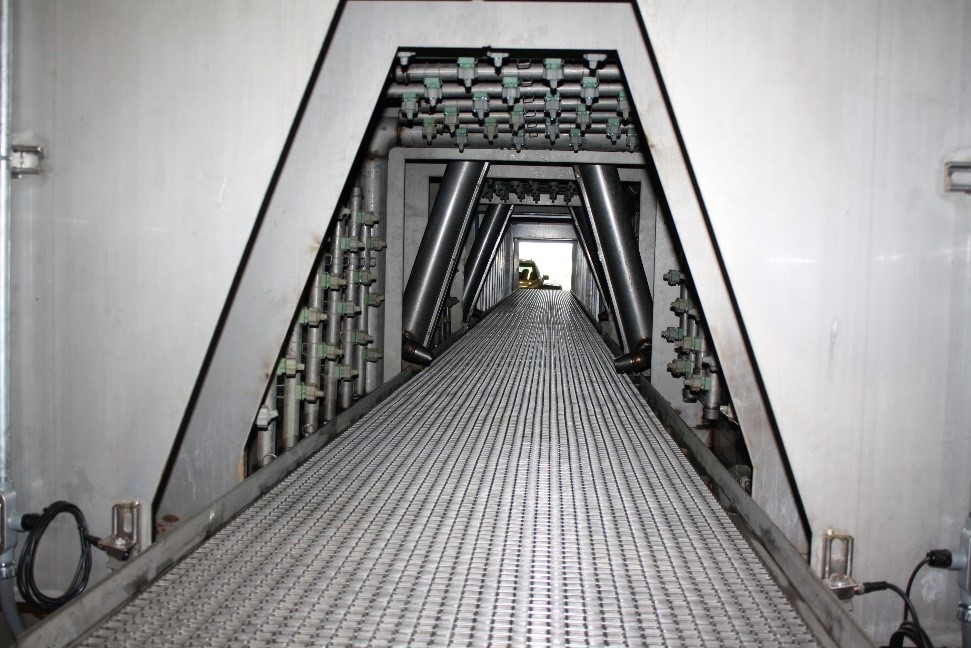
- Stainless Steel (SS) Construction – drainboards, tanks, walls, and roofs
- SS Process Piping
- SS Wetted Pumps
- SS or clip-on Polypropylene Nozzles
- SS, welded leak-tested tanks. Tank bottoms are pitched to a drain connection
- SS Tank Covers with handles and latches
- Vertical Pumps – seal-less – VFD controlled
- Header pressure is continuously monitored
- Access doors
- Screens in each tank are located in the charge box areas, before the pumps
- Optional electronic liquid level sensing and control
- Optional internal lights
- PLC with PanelView HMI – allows adjustment of nozzle flow and pressure and conveyor belt speed. Also, specific recipes can be developed and programmed, such as recipes for light, medium, and heavy parts
- Maxon, Eclipse, or Midco natural gas or propane fired burners
- Incoloy sheathed, electric, immersion heaters. Flanged connections for ease of maintenance
Conveyor Belt Washer Construction and Features
These belt conveyor spray washers utilize strategically positioned nozzles to ensure thorough cleaning and rinsing across all part surfaces. Horizon's fully integrated conveyor parts washing systems are engineered for efficiency, reliability, and minimal maintenance.
Conveyor Belt Washer Accessories
Filtering – SS bag filter housings equipped with isolation valves. Pressure monitoring is available which will provide for pressure feedback and filter cleanliness.
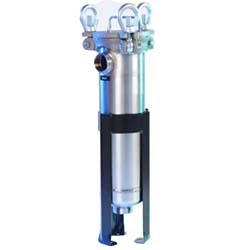
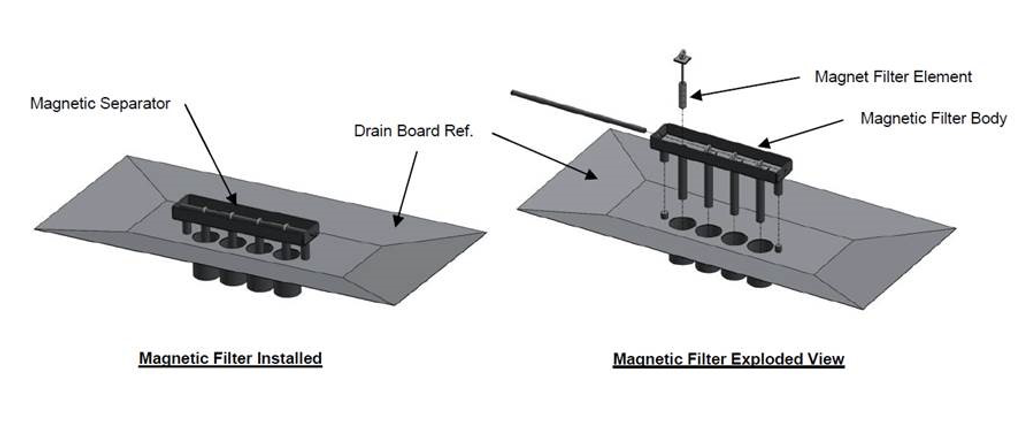
Magnetic Filter - Separator with Drain Board to eliminate magnetic fines from the cycle water. The return water passes across the magnetic filter where fines are gathered. The magnetic filter is removable from the washer.
Internal LED Lighting – A tempered glass window with LED lights mounted on the outside of the chamber. The operator can turn the lights on/off via the operator interface terminal.
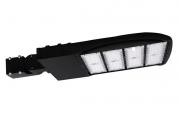
Oil Coalescer – The unit is used to remove oil from the system. The oil coalescer eliminates: Oil and greases from cleaners, high cleaning costs, frequent dumping of cleaners, bath contamination product rejects.
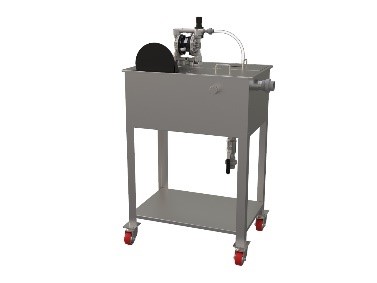
Blow-Off/Drying System – Located at the exit of the washer where water tends to collect on the product, a high-efficiency blower is used with air cannons or air knives to remove excess moisture from the products. The system is much more efficient than using compre
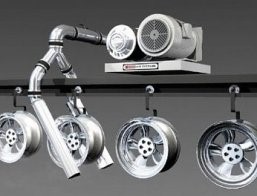
Mist Eliminator – Conserving the coating liquid is economically desirable if the washer/coater is being used for a coating process. The mist eliminator is a low-pressure drop, vane type, with SS construction, for vertical gas flow. It traps and drains a significant portion of the aerosolized coating liquid that would otherwise be carried out with the exhaust.
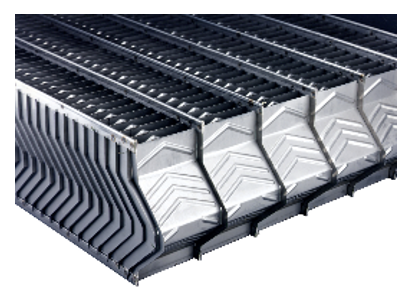
- Reverse Osmosis
- Carbon filter
- Duplex water softener
- Transfer pump
- Poly RO water storage tank
- Conductivity meter and sensor for remote monitoring of the stored water quality.
- UV light in a 316 SS housing installed in the RO storage tank recirculation line piping, for bacteria kill.
Water Treatment System – Complete Water Treatment Systems, including Reverse Osmosis (RO), are available. Using RO can reduce water consumption, improve finish quality, and decrease chemical usage. A typical Horizon Water Treatment System includes:
Our conveyor parts washers are trusted by manufacturers across a wide range of industries, from automotive to aerospace. Contact us to learn how Horizon can build the best conveyor belt washer for your specific application.
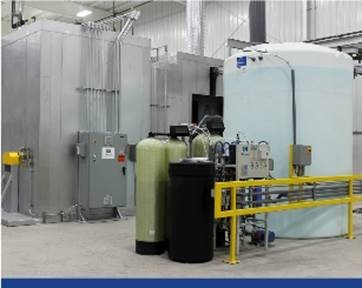
Brands
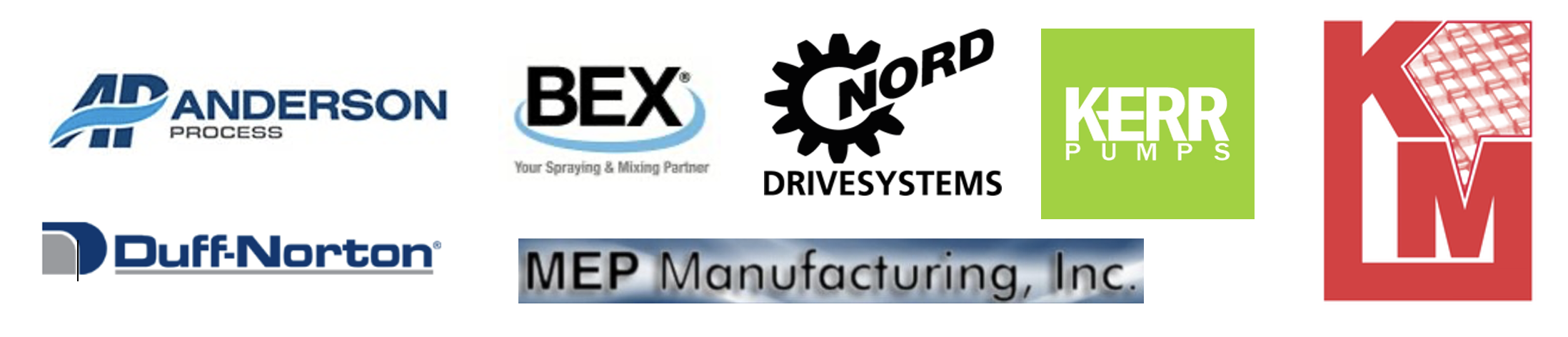