COMPOSITE CURING OVENS & PROCESSES
WHAT IS INDUSTRIAL COMPOSITE CURING?
Composite curing is a critical process in the manufacturing of composite materials, which are engineered materials made from two or more constituent materials with significantly different physical or chemical properties. The curing process involves hardening or setting the matrix material, typically a polymer resin, within the composite. This is achieved with an industrial curing oven applying heat, pressure, and/or other methods, which lead to the development of the composite’s final mechanical properties.
Why is composite Curing performed?
Solidification of the Matrix
: Curing transforms the resin from a liquid or malleable state into a solid, providing structural integrity to the composite material.Achieving Desired Mechanical Properties
: The curing process determines the final mechanical properties of the composite, such as strength, stiffness, toughness, and thermal resistance.Stabilizing the Composite Structure
: Curing ensures that the fibers or reinforcements within the composite are securely bonded within the matrix, stabilizing the overall structure.Enhancing Chemical Resistance
: Properly cured composites exhibit improved resistance to chemicals, moisture, and environmental degradation.Ensuring Dimensional Stability
: The curing process minimizes residual stresses and shrinkage, ensuring that the composite maintains its shape and dimensions over time.
Materials most commonly subjected to composite curing
Polymer Matrix Composites (PMCs)
: PMCs are the most common type of composite material, consisting of a polymer resin matrix reinforced with fibers (e.g., carbon, glass, aramid).Carbon Fiber Composites
: Carbon fibers embedded in a polymer matrix (often epoxy) create lightweight, high-strength materials.Fiberglass Composites
: Made of glass fibers reinforced with a polymer resin, such as polyester or vinyl ester.Aramid Fiber Composites (e.g., Kevlar)
: Aramid fibers provide high impact resistance and toughness when embedded in a polymer matrix.Advanced Composites (e.g., Thermoset and Thermoplastic Composites)
: These include composites with high-performance resin systems like epoxy, phenolic, or polyimide, and fibers like boron, quartz, or ultra-high-modulus carbon.
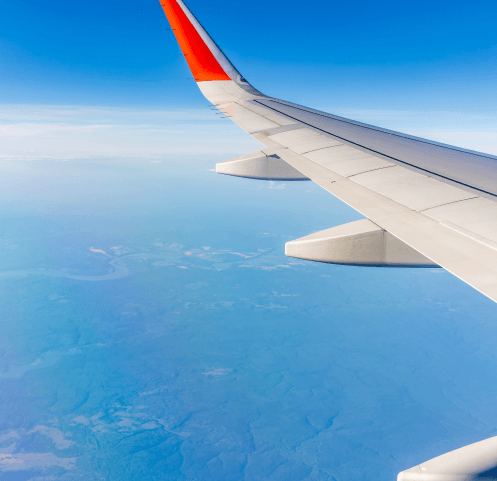
the process of composite curing with Cyclone Technology™
The composite curing process involves a series of critical steps to achieve the desired mechanical properties and durability. A Horizon industrial composite curing oven with Cyclone Technology™ revolutionizes this process by delivering precise temperature control, uniform heat distribution, and energy efficiency, outperforming traditional industrial ovens.
-
Preparation and Lay-Up: Arrange fibers and matrix material into the desired shape and orientation before curing.
-
Heating (Thermal Curing): Initiate chemical reactions in the resin, leading to cross-linking and solidification
- Cyclone Technology™ ensures unparalleled temperature uniformity of +/-3°F by employing a unique and patented airflow pattern. Unlike traditional industrial ovens, which can create uneven curing due to temperature inconsistencies with hot and cold spots, Horizon ovens maintain a uniform thermal environment, enhancing the composite's mechanical properties. This results in fewer defects and higher quality laminates, even in demanding applications
-
Pressure Application: Remove air voids, compact layers, and achieve void-free laminates.
- While Horizon Cyclone Ovens typically operate at atmospheric pressure, our superior thermal control and consistency support vacuum-bagging processes, enabling precise results without the added expense of an autoclave.
-
Gelation: Transform resin from liquid to gel, initiating hardening.
- The stable and uniform heating in Horizon Cyclone Ovens ensures that gelation occurs consistently across the entire composite. Traditional ovens may struggle with uneven gelation, leading to weak spots or uneven material properties. Cyclone Technology™ minimizes this risk
-
Final Curing: Fully solidify the resin and achieve desired mechanical properties.
- Cyclone Technology™ allows for precise control over curing profiles, ensuring optimal cross-linking and resin performance. Traditional ovens often consume more energy and require longer curing times due to less efficient heat transfer, whereas Horizon ovens reduce cycle times and energy costs without sacrificing quality.
-
Cooling: Controlled cooling to avoid thermal stresses.
- The advanced airflow design in Cyclone Technology™ facilitates controlled cooling, preventing thermal shock or warping. This ensures the composite maintains its structural integrity.
-
Demolding and Finishing: Remove the composite from the mold and prepare it for final use.
- Cured composites are demolded, trimmed, and surface-treated as required. Horizon Cyclone Ovens contribute to superior finishing quality by ensuring the composite cures uniformly, reducing the need for extensive post-curing machining or corrections
factors influencing composite Curing
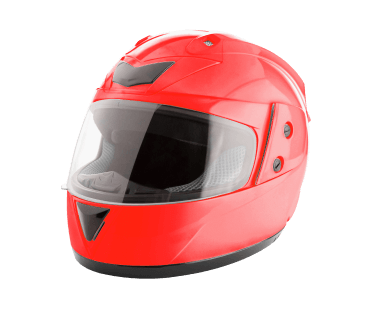
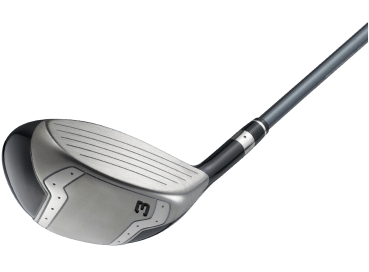
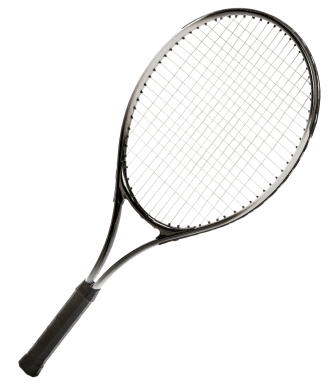
-
Material Thickness:
- Effect on Heat Transfer: Thicker composite parts require more careful control of heating rates to ensure uniform curing and to avoid overheating or under-curing in different areas.
-
Resin Type:
- Thermosetting Resins: These resins (e.g., epoxy, polyester, vinyl ester) require curing to achieve their final solid state. Once cured, they cannot be melted or reformed.
- Thermoplastic Resins: These resins can be softened by heating and reshaped, but they typically require less complex curing processes compared to thermosets.
-
Temperature:
- Curing Temperature: Different resins have specific curing temperatures. Accurate temperature control is critical to ensuring consistent properties and preventing defects.
-
Pressure:
- Autoclave vs. Atmospheric Pressure: High-performance composites often require high pressure during curing to eliminate voids and achieve optimal mechanical properties.
-
Curing Time:
- Cycle Time: The duration of the curing cycle affects the final properties of the composite. Insufficient curing time can result in incomplete cross-linking, while excessive time can lead to degradation.
-
Environmental Conditions:
- Humidity and Contamination: Environmental factors like humidity can affect the curing process, especially in sensitive materials like prepregs. Cleanroom conditions are sometimes required.
industries that utilize composite curing
Aerospace Industry
: Cured composites are used in aircraft structures, such as wings, fuselage panels, and tail sections, where high strength-to-weight ratios are essential.Wind Energy
: Composite materials are used in the manufacturing of wind turbine blades, which require a combination of strength, lightness, and durability.Automotive Industry
: In high-performance vehicles, composites are used in body panels, chassis components, and interior parts to reduce weight and improve fuel efficiency.Sporting Goods
: High-performance sports equipment, such as tennis rackets, golf clubs, and bicycle frames, is often made from carbon fiber composites for their superior strength and lightweight properties.Marine Industry
: Fiberglass composites are widely used in boat hulls, decks, and masts due to their corrosion resistance and light weight.Construction
: Composites are used in building materials, such as reinforced concrete, bridge components, and cladding systems, where durability and corrosion resistance are important.
Ready to Optimize Your Manufacturing Process?
At Horizon, we're not just building industrial ovens; we're creating solutions that drive your business forward in a cost-saving, eco-friendly way. Contact us today to discuss your needs and discover how a custom Horizon Oven with Cyclone Technology™ can revolutionize your manufacturing process!