INDUSTRIAL CONVEYOR OVENS
As one of the leading industrial conveyor oven manufacturers, Horizon designs and builds continuous process ovens engineered for consistent, high-volume production. Each conveyor system is engineered for seamless integration into your facility and optimized for maximum throughput. These systems provide significant advantages over batch ovens, particularly when uninterrupted processing is essential. The continuous flow of materials through the conveyor equipment—90% of which are belt conveyor ovens— ensures a stable environment, minimizing downtime and optimizing overall production efficiency and throughput.
Horizon Cyclone Ovens stand out for their industry-leading temperature consistency, leveraging our patented Cyclone Technology to maintain uniformity as low as +/- 2°F. This precision is critical for applications where strict heating specifications are necessary to ensure the quality of the processed parts. Multi-zoned configurations enable variable temperature profile, allowing precise heat treatment tailored to specific manufacturing needs.
Cyclone conveyor ovens are ideal for processing small to medium-sized parts that can be transported along a conveyor, with custom conveyance methods such as overhead monorail, mesh belt, chain-on-edge, chain-on-flat, slats, baskets, trays, cable, and roller conveyors available. Horizon offers both continuous and indexing conveyor belt ovens, allowing flexibility in part movement through the system. They can be tailored in size and configurations to meet the requirements of even the largest substrates in the production line.
Ready to upgrade your thermal processing? Contact Horizon today to discuss a custom conveyor ovens and a solution engineered for your goals.
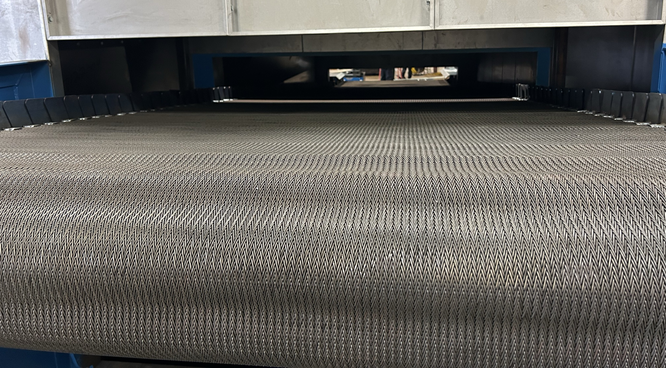
Cyclone Conveyor Ovens produce Exceptional Results for All Heating Processes
- Adhesive Curing
- Composite Curing
- Quenching
- Aging
- Drying
- Sintering
- Annealing
- Hardening
- Stress Relieving
- Burn Off
- Powder Coating
- Tempering
- Bonding
- Pre-heating
- Thermoforming
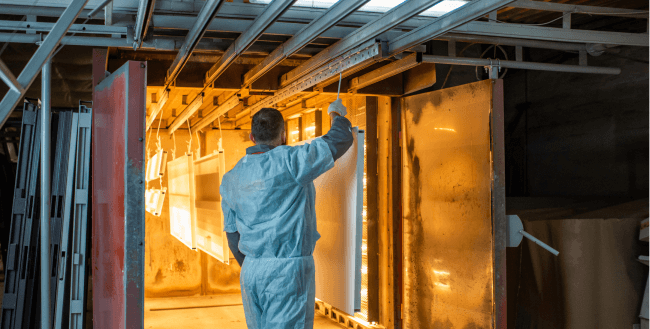
To explore how Cyclone Ovens™ support these processes, visit our Industrial Processes page.
Industries that use cyclone conveyor ovens
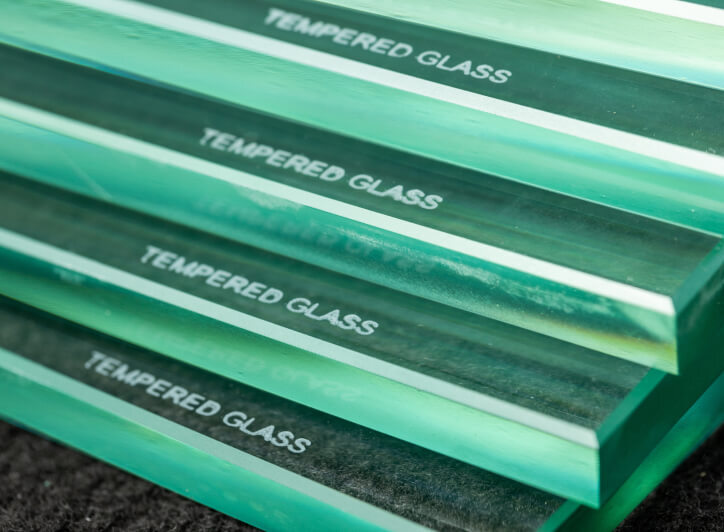
-
Aerospace:
Composite curing and high-temperature processes -
Automotive:
Curing automotive paints and heat treating metal parts -
Electronics:
Solder reflow, curing, and degassing -
Food Processing:
Baking, drying, and roasting -
Glass and Ceramics:
Tempering, annealing, and curing -
Metalworking:
Tempering, annealing, stress relieving, powder coating, and aging -
Pharmaceutical:
Sterilization, drying, and curing -
Textile and Paper:
Drying, curing, and heat setting for fabrics or paper

revolutionizing thermal processing with cyclone technology
Horizon's patented Cyclone Technology is a game-changer for the industrial conveyor oven, dramatically improving efficiency and sustainability. By optimizing airflow and temperature distribution, it significantly reduces processing times and the required oven size, saving valuable floor space. By adopting Cyclone Technology, businesses can achieve both economic and environmental goals while enhancing their production efficiency.
Key benefits of Cyclone Technology include:-
Energy Efficiency:
Eliminating traditional interior ductwork reduces airflow resistance. Enhanced insulation and extra-thick welded plate walls retain heat, lowering operating costs by minimizing heat loss through the oven walls. -
High-Efficiency Airflow:
Optimized heat transfer via high-volume, low-pressure airflow results in shorter process times and potentially smaller ovens. -
Smart Controls:
Advanced control systems with PLCs and variable frequency drives enable precise temperature and fan adjustments to match changing production loads. -
Reversible Air Recirculation:
Delivers uniform heat distribution, improving processing for sensitive products. -
Reduced Motor Horsepower:
Recirculation fans require 75–80% less horsepower, significantly cutting electricity use.
Ready to improve efficiency and performance? Contact Us to learn how Cyclone Technology can elevate your conveyor oven system.

Cyclone ovens engineered for peak performance
-
Temperature Uniformity:
Consistent oven temperature is critical for processes that ensure product strength, structural integrity, and proper coating adhesion. While temperature fluctuations challenge most ovens, Horizon’s patented Cyclone Technology minimizes variation to as low as ±2°F—an industry-leading standard. -
Heat-Up Time and Oven Size:
Cyclone ovens increase air velocity by three to six times over traditional ovens, enabling quicker heat-up and more efficient heat transfer. This can reduce oven size, conserving floor space. -
Energy Efficiency:
With lower horsepower fans, enhanced heat transfer, and compact design, Cyclone Ovens offer significant energy savings, making them both cost-effective and eco-friendly.

horizon cyclone construction surpasses conventional conveyor ovens
CONSTRUCTION
WALLS
FANS
DUCTWORK
INSULATION
horizon conveyor oven available accessories
All Horizon Cyclone conveyor ovens are equipped with advanced burners, heating elements, and customizable control systems for versatile use. In addition to your choice of oven conveyor, your oven can also be accessorized with these items and more. Need something unique? Just ask-our engineering team can build your custom solution.
- Access Ladders
- Filter Systems
- Product Baskets
- Air Cooling Chambers
- Fresh Air Preheat Systems
- Thermal Oxidizers
- Water Cooling Chambers
- PLC Controls
- Roof Safety Railings
- Cooling Chambers with Chillers



Not sure which industrial oven is right for your process?
Horizon offers a full line of industrial ovens engineered for precision and performance, including but not limited to:
Ready to Optimize Your Manufacturing Process?
At Horizon, we're not just building industrial conveyor ovens; we're creating solutions that drive your business forward in a cost-saving, eco-friendly way. Contact us today to discuss your needs and discover how a custom Horizon Oven with Cyclone Technology can revolutionize your manufacturing process!