Achieve Exceptional Results Across All Heating Processes with Cyclone Ovens™
Industries that use cyclone conveyor ovens
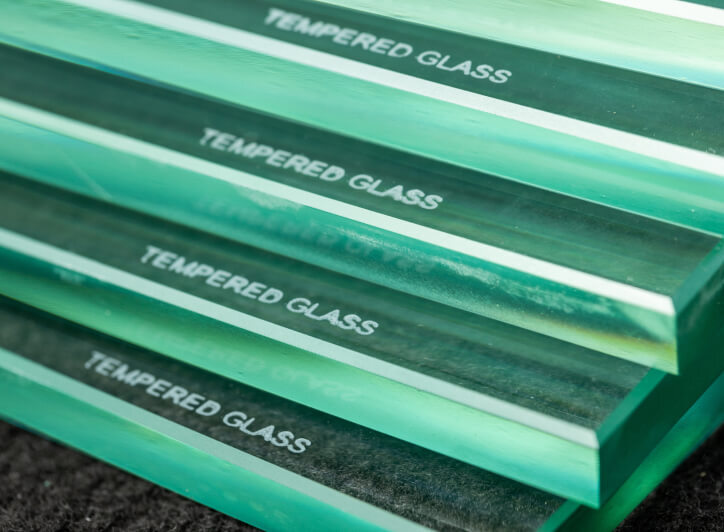
- Aerospace: Composite curing and high-temperature processes
- Automotive: Curing automotive paints and heat treating metal parts
- Electronics: Solder reflow, curing, and degassing
- Food Processing: Baking, drying, and roasting
- Glass and Ceramics: Tempering, annealing, and curing
- Metalworking: Tempering, annealing, stress relieving, powder coating, and aging
- Pharmaceutical: Sterilization, drying, and curing
- Textile and Paper: Drying fabrics or paper, curing, and heat setting

revolutionizing thermal processing with cyclone technology™
Horizon's Cyclone Technology™ is a game-changer for the industrial conveyor oven, dramatically improving efficiency and sustainability. By optimizing airflow and temperature distribution, it significantly reduces processing times and the required oven size, saving valuable floor space. By adopting Cyclone Technology™, businesses can achieve both economic and environmental goals while enhancing their production efficiency.
Key benefits of Cyclone Technology™ include:- Energy Efficiency:The elimination of traditional interior duct work in Cyclone Ovens™ minimizes airflow resistance and reduces pressure losses needed for convection heating. The enhanced insulation and extra thick welded plate walls boost heat retention and reduce energy loss. Together they significantly lower operating costs by reducing heat loss through the oven walls.
- High-Efficiency Airflow:Cyclone ovens optimize heat transfer through high-volume, low-pressure airflow, resulting in shorter process times and potentially smaller ovens.
- Smart Controls:Dependable Advanced Technology Controls feature variable frequency drives and PLC systems to allow for precise temperature and fan control in response to changing production loads.
- Reversible Air Recirculation: Cyclone Technology™ ensures uniform heat distribution and enhances process capabilities for sensitive materials.
- Reduced Motor Horsepower:75-80% less motor horsepower for recirculation fans, results in substantial electricity savings.

Cyclone ovens™: engineered for peak performance
- Temperature Uniformity: Consistent oven temperature is essential to most heat processes. Some require uniformity to guarantee product strength and structural integrity, while others need it to ensure that coatings and paints achieve optimal adhesion.Temperature fluctuations are a common challenge for most industrial ovens, but Horizon’s patented Cyclone Technology™ minimizes this issue by maintaining an internal oven temperature variation as tight as 2°F—an industry-leading standard!
- Heat-Up Time and Oven Size: Cyclone Technology™ accelerates the average air velocity surrounding the part or product to three to six times faster than traditional ovens. This results in quicker heat-up times and improved heat transfer. Faster product heating can reduce the required size of the conveyor oven, saving space with a smaller factory footprint.
- Energy Efficiency: With lower horsepower fans, enhanced heat transfer, and the potential for a more compact oven size, a Cyclone Oven™ offers significant energy savings, making it both a cost-effective and eco-friendly option.

horizon cyclone construction surpasses conventional conveyor ovens
horizon conveyor oven available accessories
All Horizon Cyclone Conveyor Ovens are equipped with advanced burners, heating elements, and customizable control systems for versatile use. In addition to your choice of conveyor equipment, your oven can also be accessorized with these items and more:
- Access Ladders
- Thermal Oxidizer w/ Heat Recovery
- Filter Systems
- Product Baskets
- Air Cooling Chambers
- Fresh Air Preheat Systems
- Thermal Oxidizers
- Water Cooling Chambers
- PLC Controls
- Roof Safety Railings
- Cooling Chambers with Chillers
- Need Something? Just ask!



Ready to Optimize Your Manufacturing Process?
At Horizon, we're not just building industrial ovens; we're creating solutions that drive your business forward in a cost-saving, eco-friendly way.Contact us today to discuss your needs and discover how a custom Horizon Oven with Cyclone Technology™ can revolutionize your manufacturing process!