INDUSTRIAL DIP TANKS
Industrial dip tank washers are used for immersion cleaning of parts. Parts are submerged in a cleaning solution to obtain complete coverage of the part. The parts can be moved, typically vertically up and down, to cause agitation of the solution for better cleaning. The solution in the tanks can also be agitated through circulation, by pumping the solution from the tank and returning it to the tank through eductors. Dip tank washers are well suited for parts with complex geometry such as blind holes or pockets that would be difficult to reach with a spray type washer. Another example would be metal tubes that must be cleaned on the inside and the outside of the tubes.
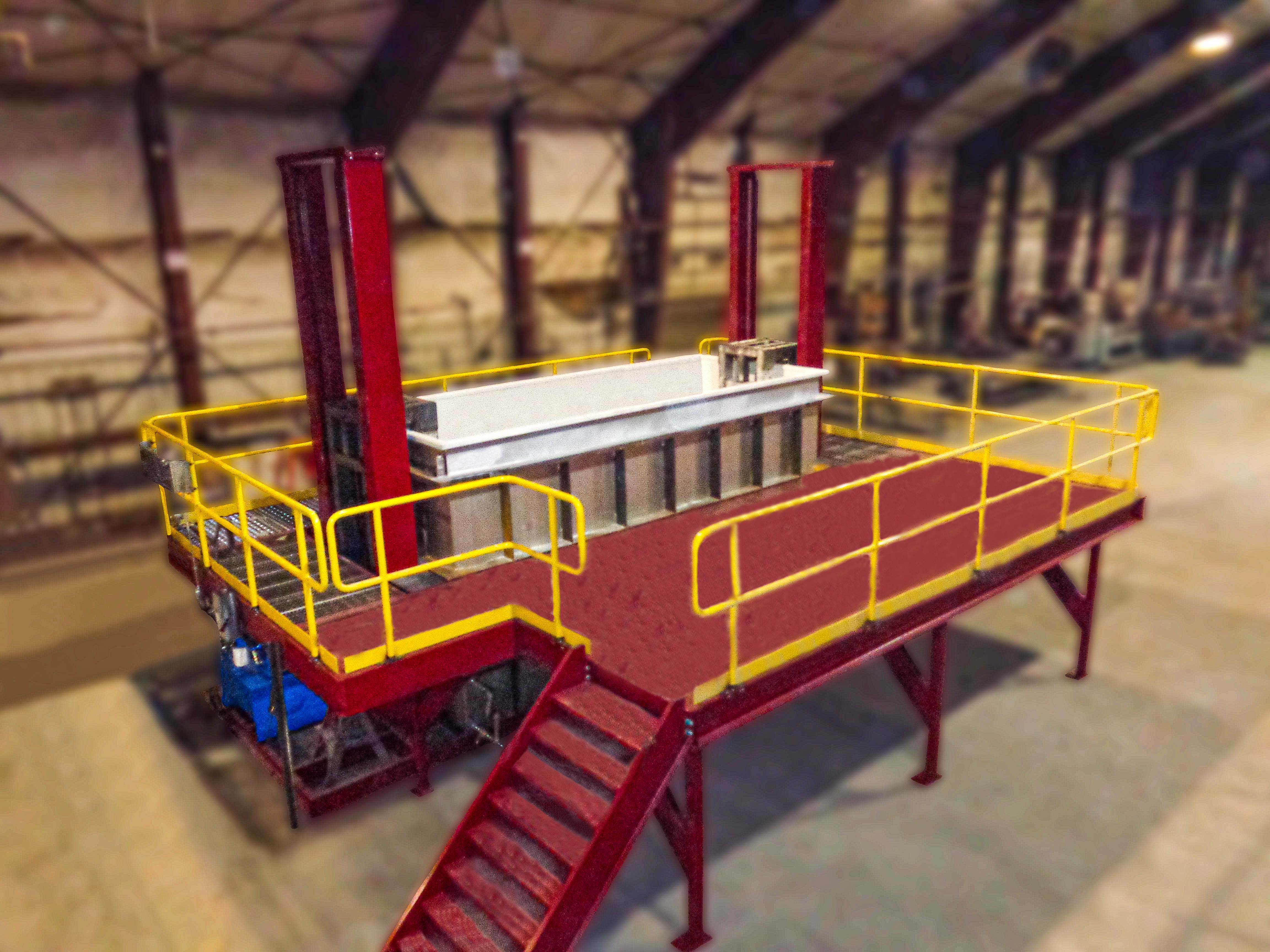
Typically, the parts are on racks, in baskets, or placed directly on a conveyor belt. Large parts may be hung individually on an overhead conveyor. A variety of conveyance methods are used, some examples are: an indexing conveyor with a vertically moving platform to lower the parts into the tank and provide part agitation, an overhead hoist lowering the part or basket of parts into the tank, or conveyor elevation changes on a continuous conveyor system lowering the parts into and raising them back out of the tank. The dip tank washer can be designed for a batch or a continuous process.
Efficiency and Innovation for Dip Tanks
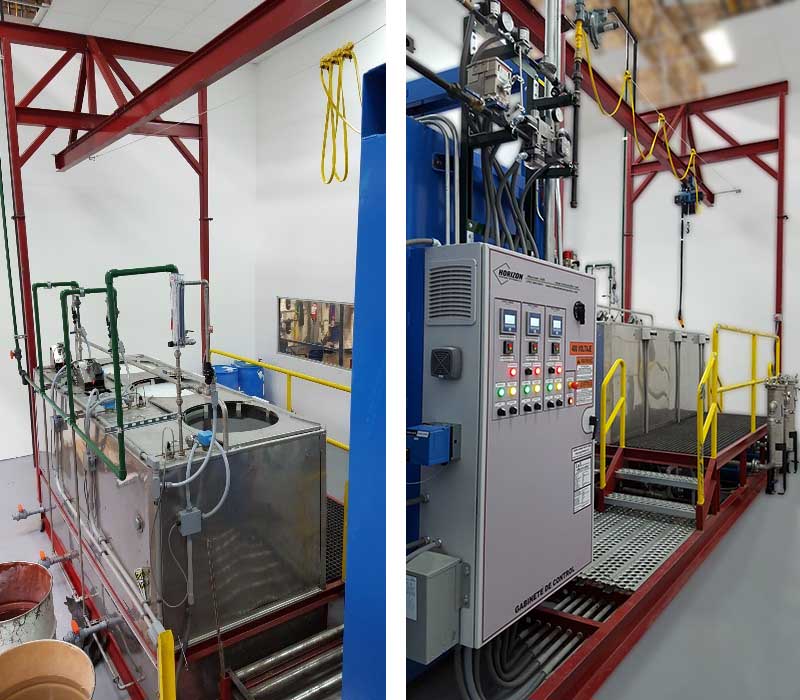
Horizon Performance Technologies has the experience and expertise to optimally design a dip tank washer for the required immersion processes in order to achieve the desired part results, along with the highest efficiency. Part geometry, part material and weight, type of solutions and processes, method of immersion, method of conveyance, angle of tank entry/exit, required dwell time, batch or continuous process, and other factors are taken into consideration during the design phase in order to obtain optimum results.
For many applications, Horizon Performance Technologies can offer its innovative tank within a tank design. The inner tank contains the parts and is filled from the bottom. The overflow from the inner tank flows to the outer tank, along with the surface oils. The parts are extracted from the inner tank which contains the cleanest solution.
Horizon Performance Technologies attention to detail and quality throughout all phases of the project, i.e., design, fabrication, installation, start-up, and post-installation follow-up, ensure the highest quality equipment and results.
- Stainless Steel Construction
- Walls, roof, drain boards, and tanks
- Piping
- Pumps
- Eductors
- Welded, leak tested tanks
- Access doors
- Optional:
- VFD pump speed control
- Header pressure monitoring
- Electronic liquid level sensing and control
- PLC with PanelView HMI
- Maxon, Eclipse, Midco natural gas or propane fired burners
- Incoloy sheathed, electric, immersion heaters. Flanged connections for ease of maintenance
Dip Tank Construction and Features
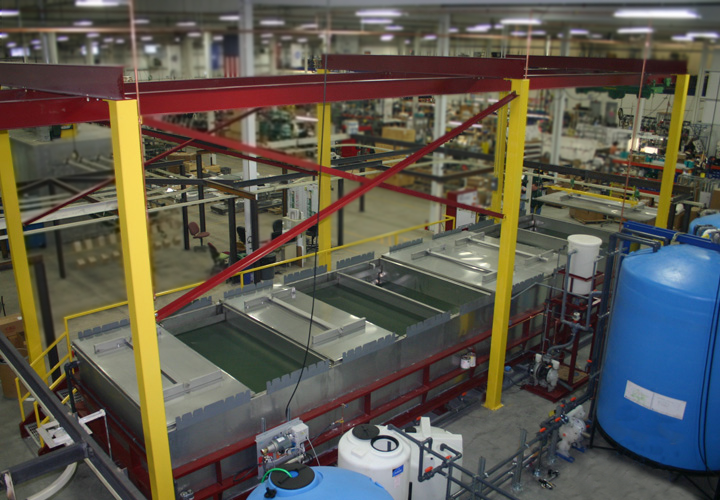
Dip Tank Accessories
Filtering – SS bag filter housings equipped with isolation valves. Pressure feedback and filter cleanliness occurs when the optional pressure monitoring is included. This can notify the operator to maintain the filter and/or shut down the system if the filter is not changed and the system falls out of spec.
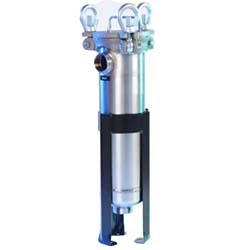
Oil Coalescer – used to process oil in two ways. The solution will be filtered and then will pass through oil separation before returning to the tank. The basic tank configuration has a solution capacity of approximately 45 gallons and is made of 14-gauge 304 stainless steel, welded water tight. The support structure also includes storage for the filter bags and placement of a 5-gallon pail for oil collection.
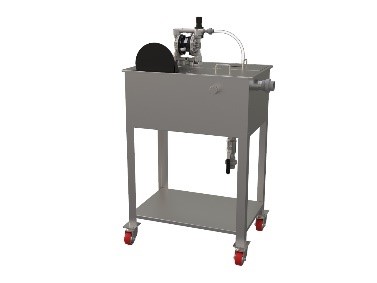
- Carbon filter, FRP tank, brass control valve, for chlorine removal from city water supply.
- Duplex water softener, FRP tanks, water meter, salt tank with salt grid and safety shutoff float, for removal of mineral hardness from the water supply.
- Reverse Osmosis machine to reduce the incoming water total dissolved solids by 97-98%. Includes: low energy membranes, permeate and concentrate flow meters, concentrate and recycle flow control valves, high pressure pump, 316 SS membrane housings, automatic inlet shutoff valve, low inlet pressure switch, inlet and outlet sample valves, pre filter – post filter – primary and final pressure gauges, 1.0 micron pre filter, powder coated steel frame, and NEMA 1 control box.
- Transfer pump to continuously circulate the stored RO water and pressurize the water going out to distribution.
- Poly RO water storage tank. Includes flow controller with internal piping to continuously circulate and mix the RO water.
- Conductivity meter and sensor for remote monitoring of the stored water quality.
- UV light in 316 SS housing installed in the RO storage tank recirculation line piping, for bacteria kill.
Water Treatment System - Complete Water Treatment Systems are available including:
Brands
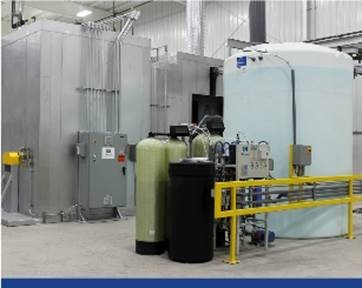
