- A pretreatment washer or a manual wash booth, or blasting equipment
- Dry-off oven
- Environmental room with powder coating booth or paint booth
- Cure Oven
- Conveyor or carts
- Controls
- Water treatment system
- Part size
- Part composition
- Weight and thickness of the parts
- Required production rate
- Means of part conveyance
- Required pretreatment chemistry (or blast equipment) - number of stages as well as time and temperature of each stage
- Spray or immersion pretreatment
- Any blow-off requirement
- Dry time and temperature
- Coating type, required thickness, required application equipment and environment
- Coating cure time and temperature
- Available footprint and height
-
Finishing systems are used in general manufacturing, aerospace, automotive, electronics, appliances, furniture, and other industries that demand reliable, high-throughput industrial finishing solutions. These paint finishing systems prepare a part for coating by pretreatment washing with a conversion coating or blasting, drying the part as necessary, applying the coating to the part, and finally curing the coating on the part. Typical components of a finishing system are:
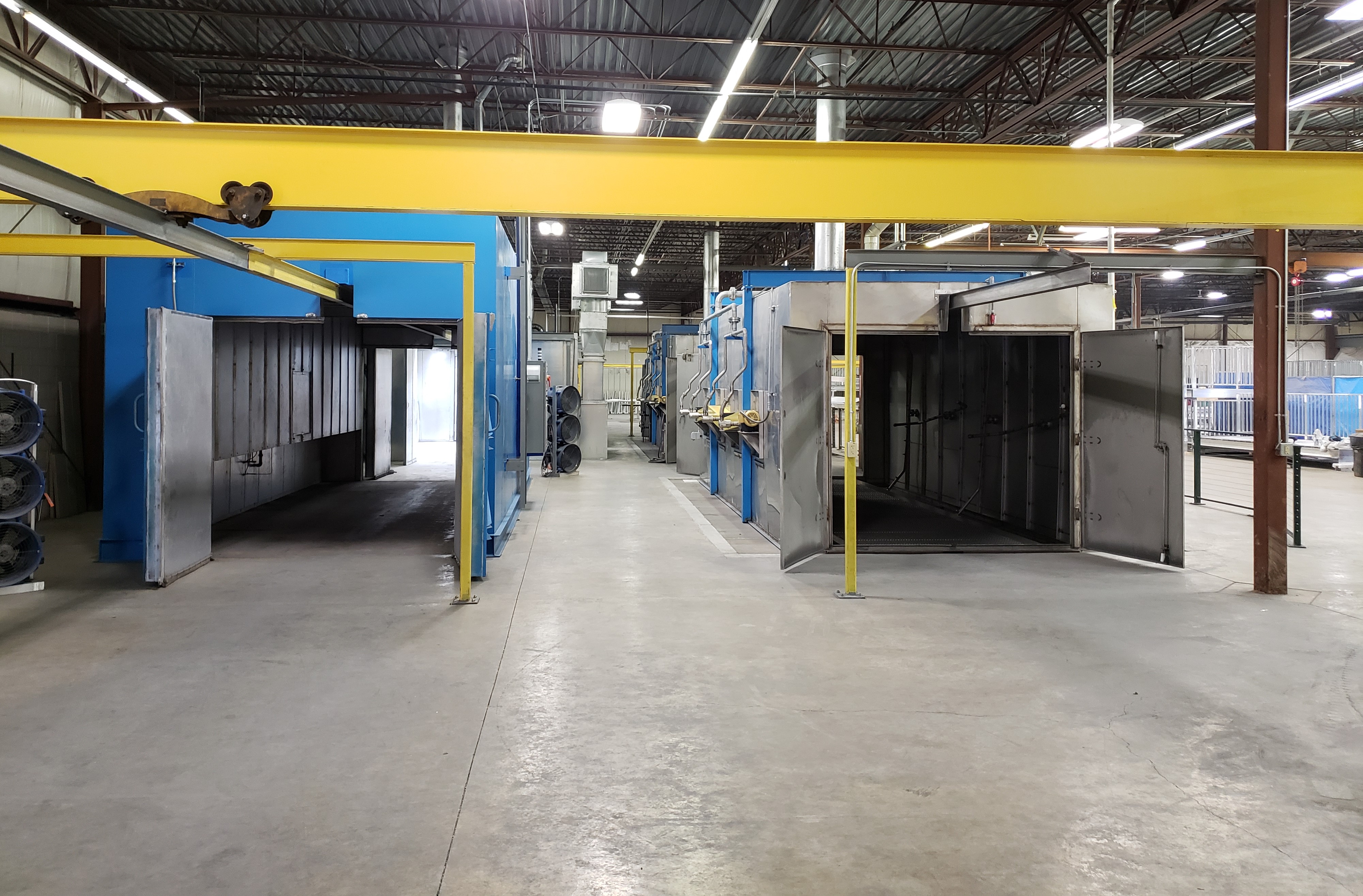
The parts can be moved through the components of the finishing system at a fixed rate via a continuous or indexing conveyor, or manually through a batch system using a manual conveyor, or a combination of both using a powered and free conveyor system. Parts can also be moved through a system manually using carts.
Factors to be considered in the design of a finishing system include:
Finishing systems are used in general manufacturing, aerospace, automotive, electronics, appliances, furniture, and other industries that demand reliable, high-throughput industrial finishing solutions.
Efficiency and Innovation for Finishing Systems
One of the most important considerations in the design of a finishing system is the layout of the equipment. The overall goal of finishing system layout and equipment design is to economically achieve the required production rate and finish quality within the available building space. Horizon Performance Technologies LLC has the experience, ingenuity, technical expertise, and patented equipment designs needed to meet customers’ needs by providing highly energy efficient and innovative finishing systems with superior performance.
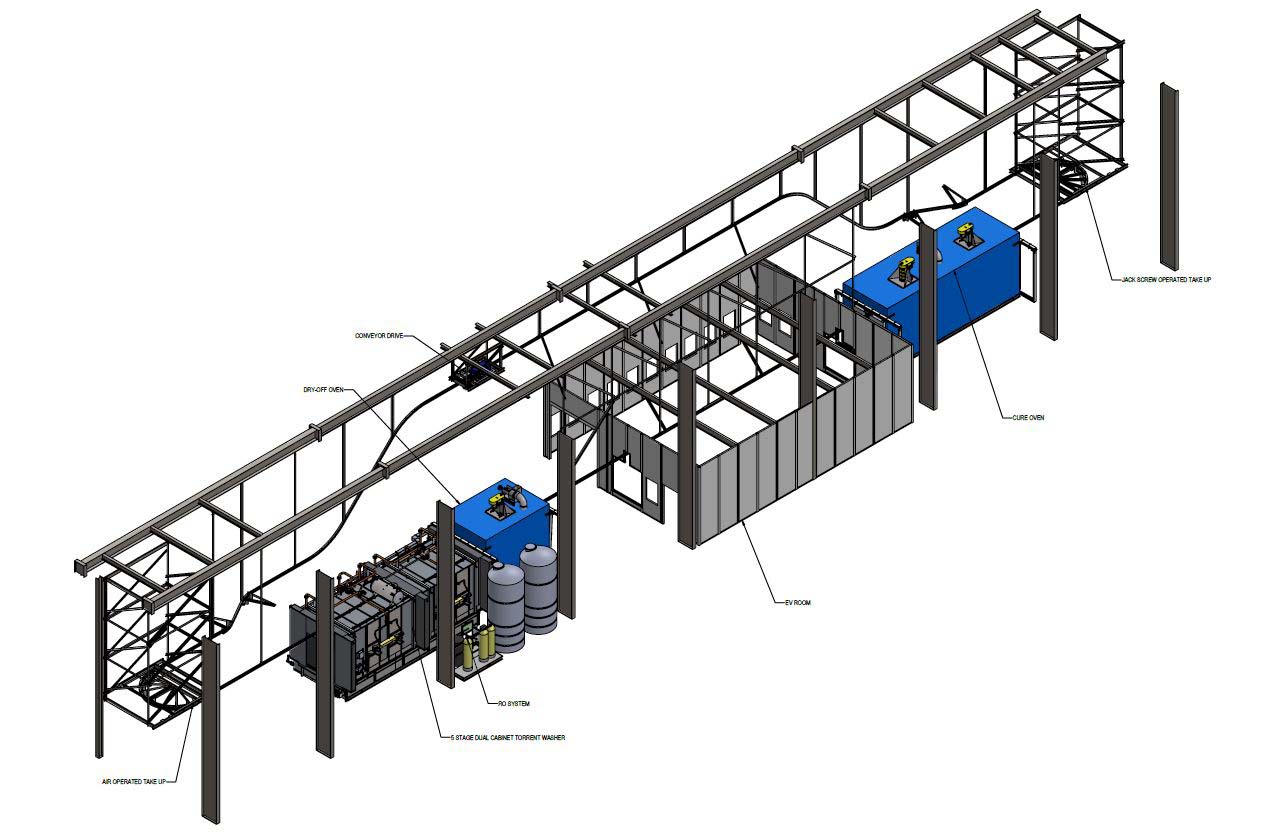
Torrent Pretreatment Washers
Patented Torrent Washers™, batch or continuous, have rotating riser bars with spray nozzles. The riser bars with nozzles move in a circular pattern while the parts are being sprayed. Traditional spray washers have stationary risers and nozzles. The Torrent Washer’s™ swirling spray pattern enables the washer’s spray coverage to cover difficult to reach areas of the parts. Another benefit of the rotation is each nozzle covers more part area, therefore significantly less nozzles are required compared to a traditional water. This results in less water flow needed for part coverage.
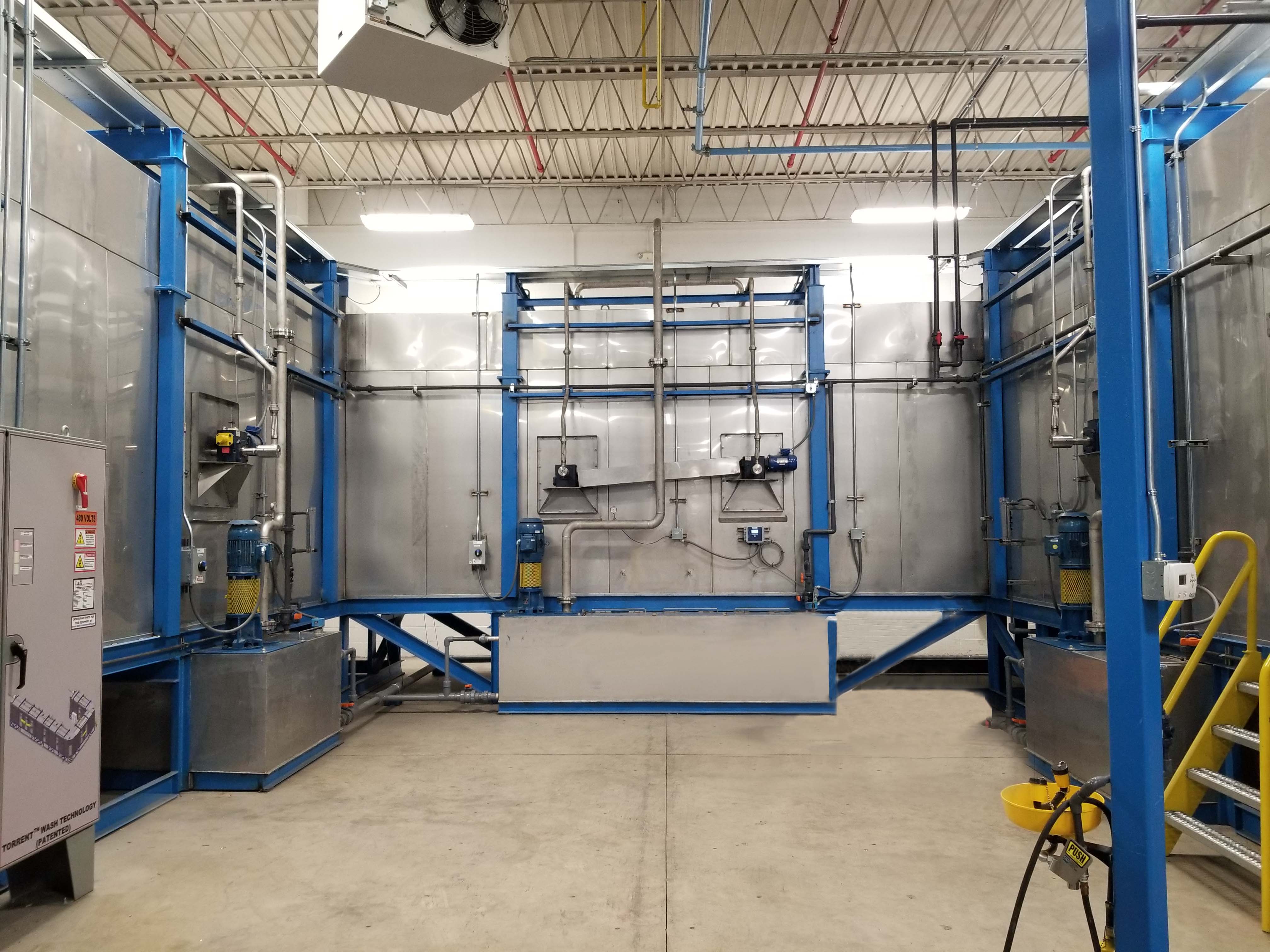
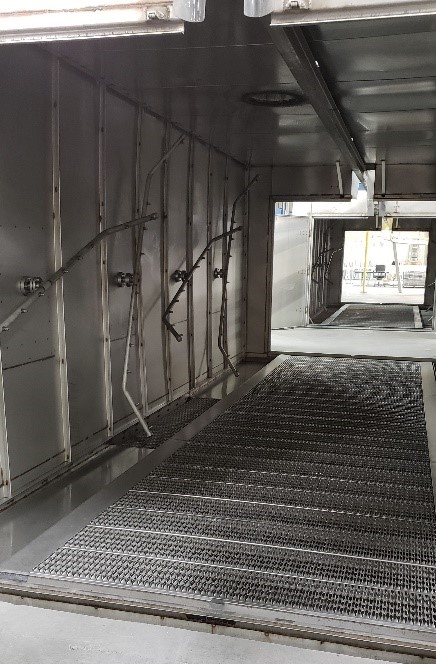
- Smaller pumps requiring less (typically 67%) electrical energy.
- Smaller tanks saving space, requiring less energy to heat, and lowering disposal costs of spent solutions.
- Reduced nozzle maintenance.
- Reduced evaporation losses.
- Superior part coverage and cleaning performance.
- Stainless steel process piping, nozzles, and wetted pumps.
- Stainless steel walls, roof, and drain boards.
- PLC with HMI controls nozzle spray pressure, nozzle arm rotational speed, and cycle times (for batch washers).
- Greater air flow with less electrical energy usage.
- VFD controlled recirculating air fans.
- All welded, 3/16” thickness exterior shell.
- Superior temperature uniformity – as low as +/- 3°F.
- Floor level burner access.
- Easily accessible interior with open floor.
- PLC with HMI enables the development of specific recipes for various part types.
Advantages of the Torrent Washer™ design:
Cyclone Industrial Ovens
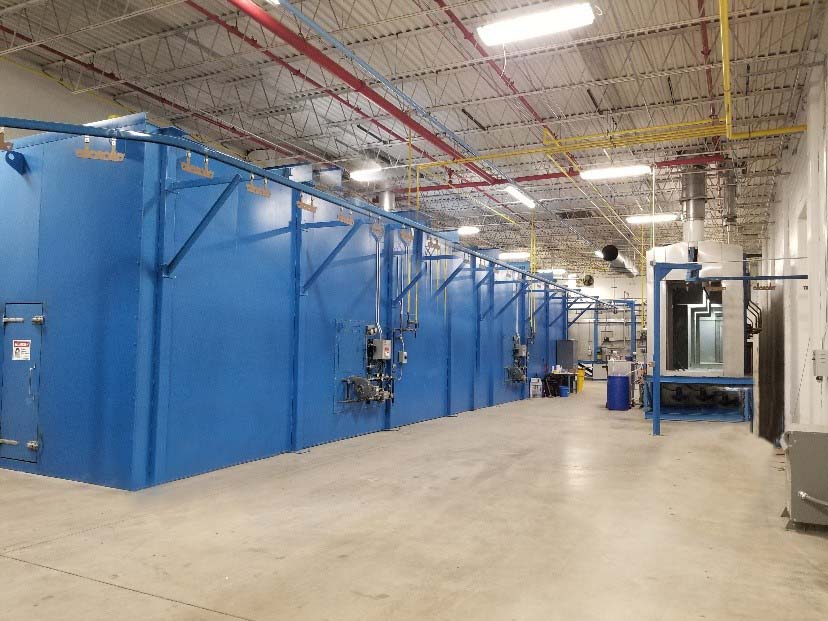
Cyclone Ovens™ also have an innovative patented design. The Cyclone Oven™ design is used in Horizon dry-off and cure ovens. They feature increased air flow, typically 1 ½ to 2 times the recirculating air flow of a traditional oven, while reducing the electric energy required. Typical electrical energy usage is half that of conventional ovens.
The increased air flow results in excellent temperature uniformity within the oven, and better heat transfer to the parts. The air flow rate is adjustable via fan motor VFDs. This allows a low flow “gel zone” and higher flow “cure zone” for powder coating.
The exterior of Cyclone ovens™ is all welded, 3/16” thickness steel. This eliminates the seam leakage found in traditional design ovens that are constructed with numerous prefabricated oven panels. Reduced seam leakage results in lower heating costs.
Advantages of the Cyclone oven™ design:
Additional Finishing System Components
In addition to Torrent Washers™ and Cyclone Ovens™, Horizon Performance Technologies offers the equipment and accessories needed for a complete finishing system:
- Enclosed track
- I-Beam
- Belt
Finishing System Conveyors
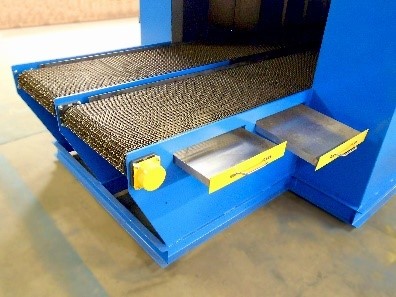
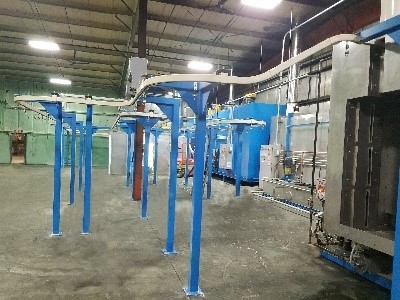
- Steel walls with acrylic enamel finish
- Suspended ceiling
- High efficiency LED lighting
- Personnel access doors with windows
- Available overhead door(s)
- Electrical outlets
Environmental Rooms
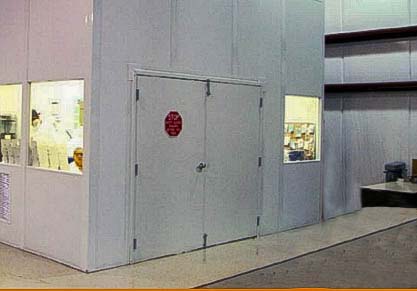
- Multiple power panels with one main control center.
- PLC with touch screen HMI located at the operator station.
- VFDs for washer pumps and oven fans interfaced to the PLC.
- Digital Temperature Controllers interfaced to the PLC.
- PLC monitors all critical safety switches.
- Remote access to HMI.
Controls
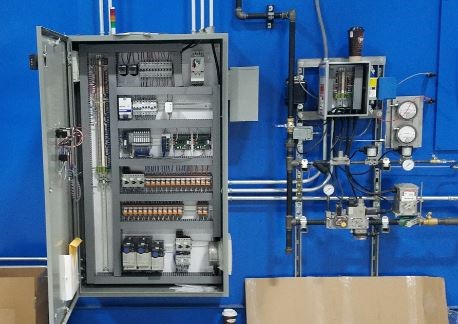
Finishing System Accessories
- Roof safety railings
- Access Ladders
- PLC controls
- Roll-up Doors under 500 degrees F
- Thermal Oxidizer
- Thermal Oxidizer with Heat recovery
Horizon Ovens
- Water Treatment Systems including Reverse Osmosis
- Carbon filter for chlorine removal
- Duplex water softener
- Reverse Osmosis machine
- Transfer pump for water circulation and pressurization to supply
- Poly RO water storage tank
- Conductivity meter
- UV light for bacteria kill
- Pretreatment Torrent Washer Accessories
- Stainless Steel Bag Filter Housings
- Magnetic Separator
- Oil Coalescer
- Zirconium Stage Filtration
- Internal LED Lighting
- Blow-Off System
- Mist Eliminator
Horizon Washers
Brands
Below are some of the brands we use for our Finishing Systems.
