Key Components of the Horizon Industrial Oven
Cyclone Ovens™ are built with best-in-class components consisting primarily of these 4 elements:
- Insulated Shell - Horizon uses a plate construction rather than the typical panel construction. This results in a stronger, “beefier” enclosure that is more structurally robust and makes for a more energy efficient industrial oven. Panel construction ovens have much more “through metal” which conducts heat from the inside to the factory environment.
-
Heating System
- Convection industrial ovens can be built with a variety of different heating media: natural gas, fuel oil, propane, electric heat, steam, thermal oil and even hot water. The choice of heating media depends on several factors, but it typically comes down to operating costs. Horizon designs custom industrial ovens with both direct and indirect heating methods, using whichever heating media best matches the requirement of the material and process.
- Direct-Fired Ovens inject the heating media directly into the oven where it mixes with the process air which carries the heat to the materials. In some cases, they can use directly fired steam. Steam is injected into the oven to heat the air and increase the relative humidity within the chamber. Direct-fired ovens are the most common type.
- Indirect-Fired Ovens keep the fuel separated from the process air. A burner firing into a tube or thermal oil being circulated through a coil are examples of indirect heating ovens. The process air contacts and takes heat from the surface of the burner tube or the coil and then delivers that heat to the parts. There are different types of burners (excess air, line burners, gun-style burners, low NOx, etc.) and different types of electric heating elements (metal sheath tubular, finned, open wound, ceramic, etc.).
-
Air Recirculation System - This system carries heat from the heat source (e.g. a gas burner or an electric heating element) to the parts being processed. Conventional Convection Ovens use medium pressure fans that blow air through ductwork to distribute heat throughout the oven chamber.
Horizon utilizes Cyclone Oven™ Technology which minimizes ductwork and uses low pressure fans to recirculate significantly larger air volumes at lower static pressures and horsepower. This results in improved air distribution, more uniform temperatures, and reduced operating costs.
-
Control System - At a minimum, the Control System for an industrial oven starts the fans, purges the oven (as required), energizes the heat source, regulates temperature and directs the safety devices. In the event of a fault, it alerts the operator and safely shuts down the oven. Horizon oven control systems are designed to meet all NFPA-86, NFPA-79, NEC and FM Insurance requirements.
Many customers also have their own operational and safety specifications which we integrate into our control platform-typically including a PLC (programmable logic controller) and HMI (human machine interface) for full operator control. In the absence of an external specification, Horizon will use only name-brand components from companies like Allen Bradly, Honeywell, Watlow, and Future Design Controls.
Need a system built around your specifications? Horizon offers component level flexibility. Start a conversation with our team and get a quote on an oven that fits your facility.
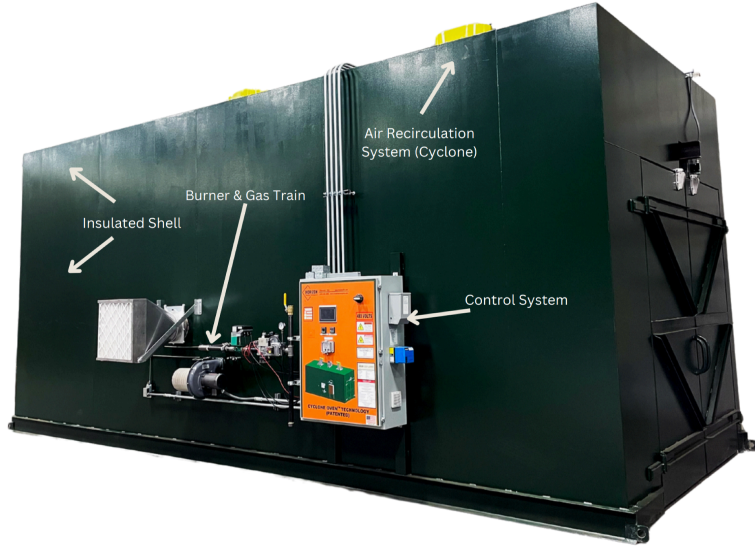
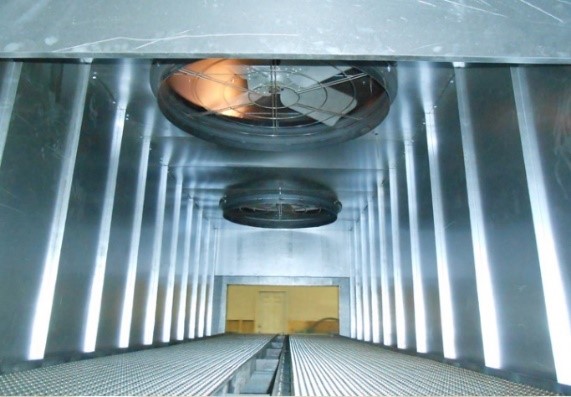
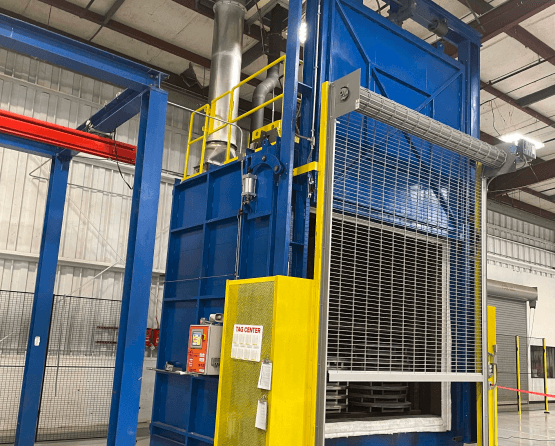
Styles of Industrial Ovens
Industrial ovens come in a wide variety of configurations to meet the diverse needs of industrial users. Ovens can be simple or they can be complicated, often categorized by the method or type of material handling associated with the oven. The most common styles include:
Walk-in Ovens: Ovens with spacious chambers designed to allow employees to physically enter the oven and place or roll large parts or racks of materials inside.
Conveyor Ovens: Perfect for continuous production lines where materials move through the oven on a conveyor belt, rollers, chains, hooks, or baskets.
Batch Ovens: Ideal for processing smaller quantities of materials in controlled batches.
1. BATCH OVENS
Horizon Industrial Batch Ovens are versatile heating units used in thermal processes such as annealing, tempering, and heat treating. As the name suggests, parts are processed in batches, meaning materials are loaded, processed, and unloaded in groups. These ovens are used in the manufacturing and finishing of a wide range of consumer and industrial goods, but are essential in industries like aerospace, automotive, electronics, and metalworking, where Horizon’s unmatched Cyclone Oven™ temperature uniformity is critical to product quality and performance.
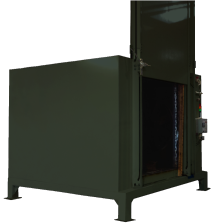
2. CONVEYOR OVENS
Horizon Industrial Conveyor Ovens are continuous processing units designed for high-volume production lines. They move products through the oven on a conveyor belt or other automated material conveyance system, allowing for consistent and efficient thermal processing. These energy efficient industrial ovens are widely used in industries like food processing, electronics, aerospace, automotive, and metal fabrication. Cyclone Technology™ enhances airflow distribution and temperature uniformity, leading to faster processing times, energy savings, reduced floor space requirements, and improved product quality.
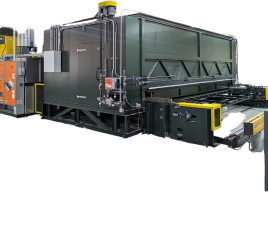
3. WALK-IN OVENS
Horizon Industrial Walk-in's are large-volume industrial ovens designed for processing over-sized or high-volume materials. These industrial ovens allow employees to walk or drive materials directly inside for various thermal processes. Commonly used in aerospace, automotive, and composites industries, they handle large parts or batches with ease. Cyclone Technology™ ensures energy efficiency and reliable performance for demanding industrial applications.
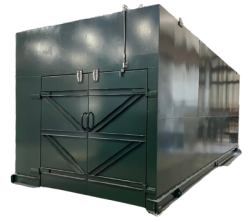
Processes Performed
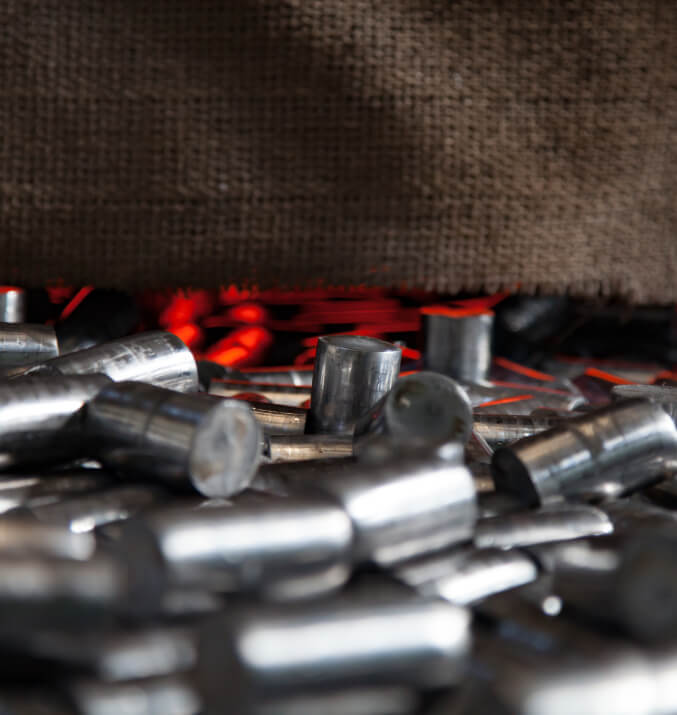
Industrial ovens are essential equipment for numerous manufacturing processes, providing precise temperature control to guarantee consistent, high-quality results.
- Preheatingmaterials before further processing
- Stress Relieving to reduce residual stresses in metals
- Temperingto enhance the toughness of materials
- Curing industrial powder coating, liquid coatings, & composites
- Dryingparts after washing or coating
- Heat Treatmentto alter the physical and mechanical properties of metals/alloys
- Annealingto reduce the hardness and increase the ductility and toughness of metals
- Bondingto join two or more materials together
- Sinteringto form a solid mass of material w/o melting it to the point of liquefaction
- Thermoforminga plastic sheet and forming it around a mold
Industries and Applications

Horizon is a trusted industrial oven manufacturer for a variety of industries including:
- Aerospace: For curing composites and heat-treating metal components
- Electronics: For drying and curing adhesives and coatings on circuit boards
- Automotive: In the production and finishing of parts like engine components and body panels
- Metalworking: In processes like annealing, tempering, and stress relieving of metal parts
Why Choose Horizon for Your Industrial Oven?
At Horizon, we are committed to designing industrial ovens that go beyond simply meeting your expectations, delivering performance that consistently exceeds them. Here's are the top three reasons Horizon should be your first choice:
Performance You Can Trust!
Horizon industrial ovens are engineered for superior performance. With our efficient Cyclone Technology™, they require smaller motors than others to achieve desired results. This can save 75% or more in electrical operating costs. Over the life of the oven, that’s a significant savings! Our celebrated temperature uniformity ensures that every part processed in our ovens meets the highest quality standards.
Beyond energy efficiency, our ovens are designed for durability and low maintenance, reducing downtime and repair costs. Whether for curing, drying, or heat treating, Horizon ovens deliver reliable, repeatable results, ensuring your production runs smoothly. Plus, with customizable configurations, we can tailor an oven solution to meet your unique process needs.
Collaborative Design Process
At Horizon, we start with a blank sheet and closely collaborate with you to build a custom industrial oven that:
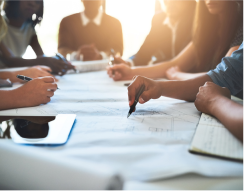
- Precisely matches your manufacturing process
- Meets your unique specifications and production rates
- Optimizes your manufacturing space with a custom design
- Can be designed with future expansion in mind
Additional Options and Features
Horizon offers a wide range of additional options to enhance the functionality of your industrial oven, including but not limited to:
- Custom conveyor systems for material handling and automated processes
- Advanced control and data collection systems with remote monitoring capabilities
- Integrated cooling zones for quicker cycle times
- Heat recovery systems that further optimize your system
- Enhanced insulation for energy efficiency
- Roof Safety Railings and Access Ladders
Ready to Optimize Your Manufacturing Process?
At Horizon, we're not just building industrial ovens, we're creating solutions that drive your business forward in a cost-saving, eco-friendly way. Contact us today to discuss your needs and discover how a custom Horizon Oven with Cyclone Technology™ can revolutionize your manufacturing process!