STRESS RELIEVING OVENS & PROCESSES
WHAT IS INDUSTRIAL STRESS RELIEVING?
Stress relieving heat treatment is a process used to reduce internal stresses within a material, typically metals, without significantly altering the material's structure. Industrial ovens play a crucial role in this process by providing a controlled environment for heating and cooling the material. This treatment is essential for improving the mechanical properties of the material, reducing the risk of distortion, and enhancing the material's performance in subsequent applications.
The Benefits of the Stress Relieving Process
Reducing Internal Stresses
: During manufacturing processes like machining, welding, casting, or forming, materials often develop internal stresses. These stresses can lead to distortion, cracking, or failure during use. Stress relieving helps to alleviate these stresses, making the material more stable.Improving Dimensional Stability
: By relieving internal stresses, the material becomes more dimensionally stable, reducing the risk of warping or distortion during subsequent machining or in-service use.Enhancing Mechanical Properties
: Stress relieving can improve the mechanical properties of a material, such as toughness and ductility, making it more suitable for demanding applications.Preventing Stress Corrosion Cracking
: In some materials, particularly certain alloys, internal stresses can make the material more susceptible to stress corrosion cracking (SCC). Metal stress relieving reduces this risk, extending the material's service life.Preparation for Further Processing
: Stress relieving is often performed as an intermediate step in manufacturing to prepare the material for further processing, such as precision machining or coating.
Material Most Commonly Subjected to stress relieving
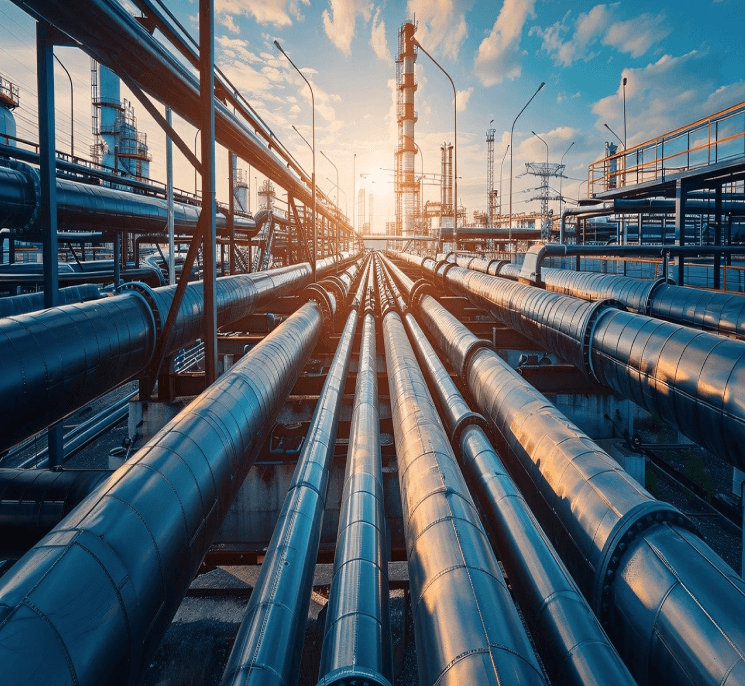
-
Metals:
- Carbon Steel and Alloy Steel: Widely stress-relieved to reduce internal stresses after processes like welding, machining, or casting.
- Stainless Steel: Often stress-relieved to improve resistance to stress corrosion cracking and to enhance mechanical properties.
- Aluminum: Stress relieving is used to prevent distortion and improve dimensional stability, particularly after machining or welding.
- Copper and Brass: Stress relieving is performed to enhance ductility and reduce the risk of cracking, especially in parts that undergo significant forming or bending.
-
Glass:
- Stress relieving, also known as annealing in glass, is used to reduce internal stresses created during shaping or forming, improving the material’s strength and durability.
-
Plastics and Polymers:
- Certain high-performance plastics and composites may undergo stress relieving to reduce internal stresses from molding or machining, improving dimensional stability and performance.
-
Welded Assemblies:
- Welded structures, especially those made from steel, are often stress-relieved to prevent distortion, cracking, and to improve the overall structural integrity.
cyclone technology™ and industrial stress relieving
Cyclone Technology™ significantly enhances every step of the stress relieving process by optimizing heat transfer, energy efficiency, and uniformity.
-
Loading the Material
- Challenge: Uneven heating can cause sagging or warping.
- Cyclone Enhancement: Cyclone Technology™ ensures even heat distribution by creating a turbulent air or gas flow within the oven chamber. This turbulence eliminates hot or cold spots, ensuring that all parts of the material are exposed to uniform temperatures from the start, regardless of placement.
-
Heating to the Target Temperature
- Challenge: Rapid or uneven heating can induce thermal shock.
- Cyclone Enhancement: The controlled circulation of heated air allows for precise temperature ramp-up rates. This controlled heating minimizes temperature gradients across the material, reducing the risk of thermal shock while achieving faster and more energy-efficient heating.
-
Soaking at the Target Temperature
- Challenge: Maintaining consistent temperature throughout the material's thickness and surface.
- Cyclone Enhancement: Cyclone Technology™ ensures that heat is consistently applied across every part of the material during the soaking phase. The enhanced convection currents promote deeper heat penetration and more uniform internal stress redistribution, even for thicker components.
-
Cooling
- Challenge: Rapid or uneven cooling can reintroduce stresses or cause cracking.
- Cyclone Enhancement: The same uniform airflow principle applies during the cooling phase. Cyclone Technology™ allows precise control over cooling rates, ensuring gradual (10-20°C), consistent cooling that prevents re-stressing or cracking. In applications requiring an inert atmosphere, Cyclone Technology ensures even gas flow to minimize oxidation risks.
-
Post-Process Inspection
- Challenge: Defects or distortions from uneven heating or cooling.
- Cyclone Enhancement: By preventing distortions during the stress-relieving process, Cyclone Technology™ reduces the likelihood of defects, resulting in a more stable, defect-free material. This consistency minimizes rework and enhances product quality.
Energy efficiency is also a challenge when performing heat stress relieving in an industrial oven. The process can often be quite energy-intensive. Efficient design and operation, including the use of insulation, heat recovery systems, and precise control mechanisms, are essential for minimizing energy consumption and reducing operational costs. Cyclone Technology™ reduces energy consumption by optimizing heat transfer rates and minimizing heat loss. Improved thermal dynamics also mean faster heating and cooling times without compromising quality.
industries that use Industrial Stress Relieving
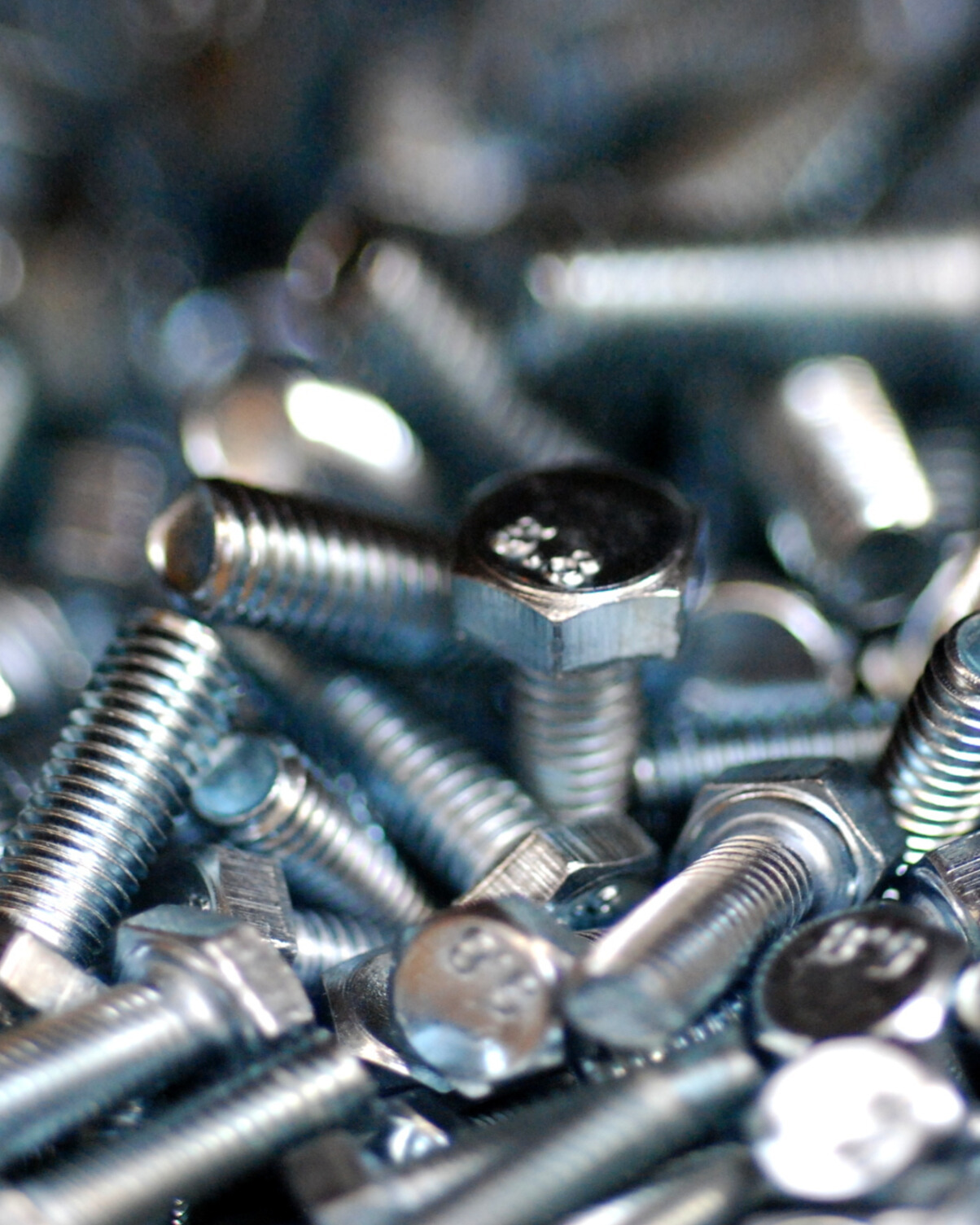
-
Automotive:
Stress relieving is used for various components, such as engine blocks, gears, and structural parts, to ensure dimensional stability and prevent failure during operation. -
Aerospace:
Aerospace components, often made from high-performance alloys, undergo stress relieving to enhance mechanical properties and ensure reliability under extreme conditions. -
Construction and Structural Steel:
Structural steel components, beams, and welded assemblies are stress-relieved to prevent distortion and ensure long-term stability in buildings and infrastructure. -
Tool and Die Manufacturing:
Tool steels and dies are stress-relieved to prevent cracking and to improve wear resistance during use. -
Oil and Gas:
Pipes, fittings, and pressure vessels used in the oil and gas industry are stress-relieved to reduce the risk of failure in harsh environments. -
Power Generation:
Components used in power plants, such as turbines, boilers, and pressure vessels, are stress-relieved to ensure they can withstand high temperatures and pressures without deforming or failing. -
Medical Devices:
Instruments, implants, and diagnostic equipment must all meet precise standards and maintain tight tolerances. Stress relieving helps ensure their reliability.
Ready to Optimize Your Manufacturing Process?
At Horizon, we're not just building industrial ovens; we're creating solutions that drive your business forward in a cost-saving, eco-friendly way. Contact us today to discuss your needs and discover how a custom Horizon Oven with Cyclone Technology™ can revolutionize your manufacturing process!