TEMPERING PROCESS & OVENS
WHAT IS TEMPERING?
Tempering is a heat treatment process applied to metals, particularly steels, to enhance their mechanical properties by improving toughness and reducing brittleness. After hardening, materials often become very hard but also brittle, which can lead to failure under stress. Tempering metal reduces brittleness while maintaining the hardness and strength of the material. Industrial tempering ovens provide a controlled environment for the precise heating and cooling required during tempering.
Why is tempering performed during the Manufacturing Process?
-
Improve Toughness
: Tempering steel increases its toughness, allowing it to absorb energy and resist impact without fracturing. This is crucial for materials used in dynamic or high-stress environments. -
Relieve Internal Stresses
: The hardening process can introduce internal stresses into the material, which can cause distortion or cracking. Tempering hardened steel relieves these stresses, stabilizing the material's structure. -
Reduce Brittleness
: Hardening processes like quenching can leave steel extremely hard but also brittle, making it susceptible to cracking. Tempering reduces this brittleness, improving the material's toughness and making it more durable. -
Adjust Hardness
: Tempering allows for precise control over the final hardness of the material. By adjusting the tempering temperature and time, manufacturers can achieve the desired balance between hardness and toughness. -
Enhance Wear Resistance
: In some situations, tempering can enhance the wear resistance of the material by refining the microstructure and improving the distribution of carbide particles within the steel.
Material Most Commonly tempered
-
-
Carbon Steel
- Carbon steel is commonly tempered after hardening to reduce brittleness and improve toughness. The exact tempering temperature depends on the desired balance between hardness and toughness.
-
Alloy Steel
- Alloy steels, which contain additional elements like chromium, nickel, or molybdenum, are often tempered to optimize their mechanical properties for specific applications.
-
Tool Steel
- Tool steels, used for cutting, shaping, and forming tools, are tempered to achieve a balance between hardness and toughness, making them durable under high stress.
-
Stainless Steel
- Certain grades of stainless steel, especially martensitic stainless steel, are tempered to improve corrosion resistance and toughness after hardening.
-
Cast Iron
- Some types of cast iron, such as malleable iron, undergo tempering to improve ductility and reduce brittleness.
-
Non-Ferrous Alloys
- Includes titanium alloys and copper alloys (bronze and brass), tempering adjusts the alloy’s hardness and stress resistance. It also improves fatigue resistance.
-
Superalloys
- Superalloys contain elements like nickel, cobalt, and iron which are used in extreme environments. Tempering increases heat and oxidation resistance.
-
Glass
- While not a metal, glass is commonly tempered strengthening it and making it shatter-resistant for use as safety glass in automotive windows, electronics, etc.
-
Spring Materials
- Spring steel, used in automotive suspensions and industrial machinery, is tempered to enhance elasticity and fatigue resistance.
industrial Tempering utilizing cyclone technology
Cyclone Technology introduces advanced airflow dynamics to address the limitations of traditional metal tempering oven processes. Using high-velocity, precisely controlled air circulation, it ensures optimal heat transfer and uniform temperature distribution.
-
Temperature Uniformity
- Challenge: Traditional ovens often struggle with temperature gradients, leading to uneven material properties.
- Solution: Cyclone Technology ensures consistent airflow throughout the oven, eliminating hot and cold spots. This uniformity prevents over- or under-tempering of certain areas, resulting in a product with consistent mechanical properties.
-
Faster Cycle Times
- Challenge: Slow heating and cooling rates increase processing times and reduce throughput.
- Solution: The high-velocity airflow in Cyclone Technology improves heat transfer, reducing the time required to reach and maintain the desired tempering temperature. Similarly, cooling is accelerated with controlled air patterns, shortening the overall process cycle.
-
Enhanced Energy Efficiency
- Challenge: Poor thermal distribution leads to wasted energy and higher costs.
- Solution: By optimizing airflow, Cyclone Technology reduces energy consumption. Heat is more effectively utilized, and fewer resources are needed to maintain the required temperature.
-
Minimized Thermal Stress
- Challenge: Uneven or rapid heating and cooling can reintroduce stresses or deform the material.
- Solution: Controlled, uniform airflow prevents thermal gradients, minimizing the risk of cracking, warping, or distortion. Materials retain their integrity and dimensional stability.
-
Improved Product Quality
- Challenge: Variations in temperature control lead to inconsistent mechanical properties.
- Solution: Cyclone Technology ensures precise temperature control during heating, soaking, and cooling. The resulting product exhibits uniform hardness, toughness, and ductility, enhancing performance and reliability.
-
Adaptability for Different Materials
- Challenge: Different materials and applications require specific tempering parameters.
- Solution: Cyclone Technology offers customizable airflow settings to accommodate various material types and geometries, making it suitable for a wide range of industrial needs.
applications for industrial tempering
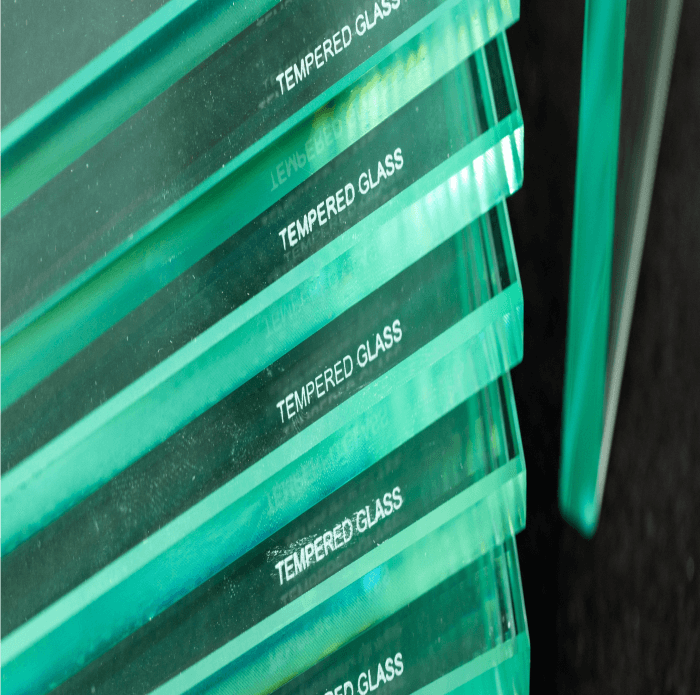
-
Automotive
: Components like gears, shafts, springs, and fasteners are tempered to ensure they can withstand the stresses and strains of automotive use. Auto glass is tempered to make it less resistant to shattering. -
Aerospace
: Aerospace components, often made from high-strength steels and alloys, are tempered to achieve the necessary balance of toughness, hardness, and resistance to fatigue. -
Tool and Die Manufacturing
: Tools such as drill bits, dies, punches, and cutting tools are tempered to maintain sharpness and durability during use. -
Construction
: Structural steel components, such as beams and supports, may be tempered to improve their load-bearing capacity and resistance to impact. -
Oil and Gas
: Tempering is used in the manufacturing of pipelines, valves, and drilling equipment to enhance their strength and resistance to wear in harsh environments. -
Defense and Military
: Components for military vehicles, weapons, and armor are tempered to ensure they can withstand extreme conditions and impacts.
Ready to Optimize Your Manufacturing Process?
At Horizon, we're not just building industrial tempering ovens; we're creating solutions that drive your business forward in a cost-saving, eco-friendly way. Contact us today to discuss your needs and discover how a custom Horizon Oven with Cyclone Technology can revolutionize your manufacturing process!