THERMOFORMING PROCESS & OVENS
WHAT IS THERMOFORMING?
Thermoforming is a manufacturing process where a plastic sheet is heated until pliable, shaped into a specific form using a mold, and trimmed to create a finished product. This process is widely used for producing lightweight, durable, and cost-effective parts across a variety of industries. Its versatility allows manufacturers to create products with intricate shapes and details, making it ideal for applications requiring precision and customization. Additionally, thermoforming supports a range of material options, enabling tailored solutions for specific performance requirements.
the Benefits of Thermoformed Materials
-
Cost-Efficiency
: Tooling and production costs are lower with thermoforming as compared to other forming methods. -
Flexibility
: Due to its relatively simple and low-cost tooling requirements, thermo allows for rapid prototyping and design modifications due to its relatively simple and low-cost tooling requirements compared to processes like injection molding. -
Scalability
: Thermoforming is Ideal for both small and large production runs due to its cost-effective and scalable nature. For small runs it offers inexpensive molds, quick setup/changeovers, and unique or customized designs without the high costs of other methods. For large production runs, modern thermoforming equipment enables high-speed production, minimizes material waste through continuous processes like roll-fed systems, and utilizes durable tooling to maintain efficiency and quality over long-term use. -
Material Versatility
: Thermoforming offers material versatility, working with a wide range of plastics. This flexibility allows manufacturers to choose materials that meet specific application requirements, from durability to aesthetic appeal.
materials most commonly used for thermoforming
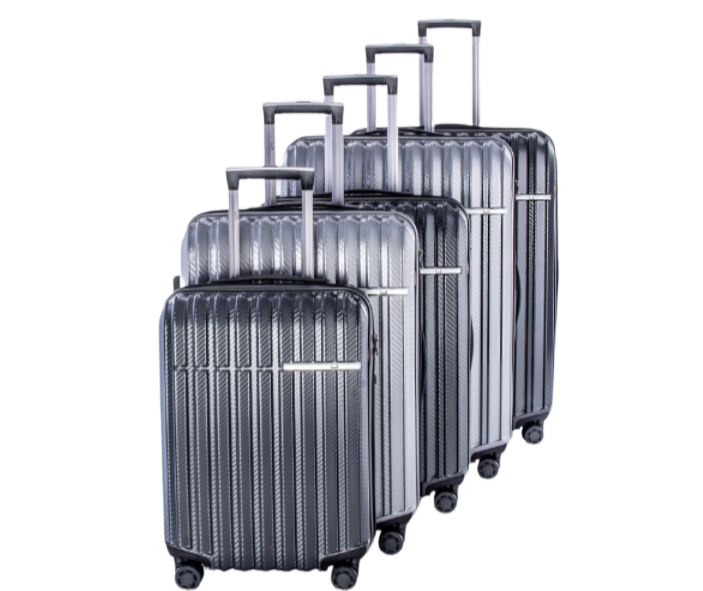
-
Acrylic (PMMA)
- Polymethyl methacrylate is a synthetic resin known for its clarity and impact resistance. It is often used as a substitute for glass in products such as shatterproof windows, illuminated signs, and aircraft canopies.
-
Polypropylene (PP)
- Polypropylene is a common thermoplastic polymer. It is lightweight and resistant to chemicals, moisture, and flames.
-
Polyethylene (PE)
- Polyethylene is the most prevalent plastic. It’s durable and commonly used for packaging, plastic bags, containers, and bottles.
-
Polystyrene (PS)
- Polystyrene is a synthetic polymer. It can be used solid or foamed and is an inexpensive resin.
-
ABS (Acrylonitrile Butadiene Styrene)
- ABS is an opaque thermoplastic. It is tough and ideal for structural components.
The Thermoforming Process and Horizon Cyclone Oven Benefits
Experience precision and performance at every stage of plastic thermoforming with Horizon’s Cyclone Technology. From uniform heating to efficient cooling, our advanced system ensures consistent quality, faster cycles, and reliable results—even for complex shapes.
-
Heating the Plastic Sheet
- Process: The sheet is evenly heated to a specific temperature to become pliable without degrading its properties.
- Horizon Advantage: Cyclone Technology delivers uniform heat distribution, reducing hot spots and ensuring consistent material quality.
-
Shaping the Plastic with a Mold
- Process: The heated sheet is placed over or into a mold, where vacuum, pressure, or mechanical force is applied to form the desired shape.
- Horizon Advantage: Precise temperature control minimizes warping and ensures accurate mold conformance, especially for complex shapes.
-
Cooling and Trimming the Formed Part
- Process: The shaped part is cooled to retain its new form and trimmed to remove excess material.
- Horizon Advantage: Optimized airflow enhances cooling efficiency, speeding up production cycles and maintaining part integrity.
-
Post-Processing (Optional)
- Process: Additional finishing steps, such as painting, assembly, or surface treatments, may be performed.
- Horizon Advantage: Consistent output quality reduces the need for extensive finishing, saving time and resources.
Industries that benefit from industrial thermoforming
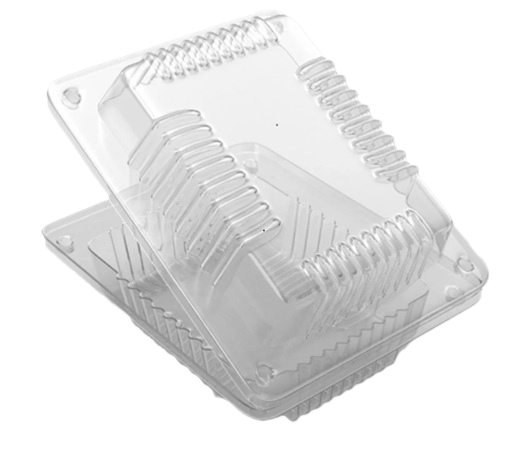
-
Automotive
: Interior panels, dashboards, and protective covers -
Packaging
: Food containers, blister packs, and clam shell packaging -
Medical
: Custom trays, device housings, and sterile packaging -
Construction
: Wall panels, skylights, and decorative elements -
Aerospace
: Lightweight interior panels and components -
Consumer Goods
: Household items, toys, and appliance parts -
Industrial Equipment & Electronics
: Equipment housings and panels, shipping trays for electronics
Ready to Optimize Your Manufacturing Process?
At Horizon, we're not just building an industrial thermoforming oven; we're creating solutions that drive your business forward in a cost-saving, eco-friendly way. Contact us today to discuss your needs and discover how a custom Horizon Oven with Cyclone Technology can revolutionize your manufacturing process!