Why is preheating performed during the Manufacturing Process?
- Material Properties Optimization: Many materials, including metals, plastics, and composites, have specific temperature ranges where their properties are most favorable for processing. Preheating brings the material to this range, ensuring better workability, bonding, and performance.
- Thermal Stress Reduction: Sudden exposure to high temperatures during processing can induce thermal stresses in materials, leading to warping, cracking, or other defects. Preheating gradually raises the temperature, minimizing these risks.
- Improved Adhesion and Coating: In processes like powder coating or painting, preheating helps in improving the adhesion of coatings by removing surface moisture, contaminants, and ensuring uniform coating application.
- Energy Efficiency: Preheating can lead to more efficient energy use in subsequent processes. For example, preheated materials require less energy to reach the desired temperature for forging or molding, thus saving energy.
- Process Consistency: Preheating ensures consistent processing conditions, leading to uniformity in product quality, which is crucial in mass production environments.
Materials most commonly subjected to preheating
- Metals: Steel, Aluminum, Copper are commonly preheated before processes like forging, welding, or extrusion to improve workability and reduce the risk of thermal stress. Galvanized Metals are often preheated before powder coating to ensure proper adhesion and prevent defects.
- Plastics and Polymers: Thermoplastics are preheated before molding or forming to reduce cycle times and improve material flow. In Composite Materials, preheating is used to remove moisture and reduce the risk of voids during curing or laminating.
- Glass: Preheating is essential in glass manufacturing and processing to prevent thermal shock and ensure uniformity in subsequent shaping or tempering processes.
- Rubber: Rubber Compounds are preheated before vulcanization or molding to enhance flow and ensure uniform curing.
- Wood: MDF and Plywood: Preheating removes moisture and reduces internal stresses before laminating or coating, improving the quality of the final product.
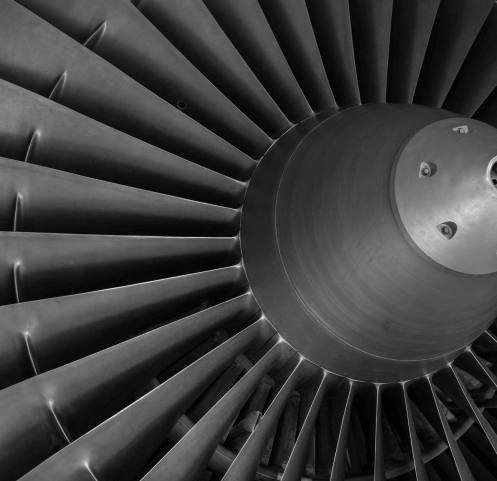
the benefits of Cyclone technology in the Preheating process
Cyclone Technology™ brings transformative benefits to the preheating process, ensuring precision, efficiency, and safety at every step. By leveraging advanced airflow management, it delivers uniform heat distribution and optimized energy use, addressing critical challenges in industrial applications. This innovative approach enhances productivity while supporting sustainability and reducing operational risks.
- Precise Temperature Control: Cyclone Technology™ ensures accurate temperature regulation by continuously adjusting airflow and monitoring heat distribution. This is critical for materials prone to thermal degradation or requiring strict adherence to temperature parameters.
- Optimized Heating Time: High-velocity airflow accelerates heat transfer, reducing the time needed to achieve target temperatures. This increases productivity and minimizes energy use.
- Enhanced Energy Efficiency: By maximizing heat transfer efficiency and minimizing energy loss, Cyclone Technology™ significantly reduces operational costs. Features such as heat recovery and advanced insulation further improve sustainability.
- Superior Atmosphere Control: For processes requiring controlled environments (e.g., inert gas or vacuum), Cyclone Technology™ maintains consistent airflow and temperature stability, preventing oxidation or contamination.
- Improved Safety: Cyclone Technology™ enhances safety through precise thermal management and reliable airflow control. This reduces risks of overheating, equipment damage, and operator exposure to unsafe conditions.
industries that utilize preheating
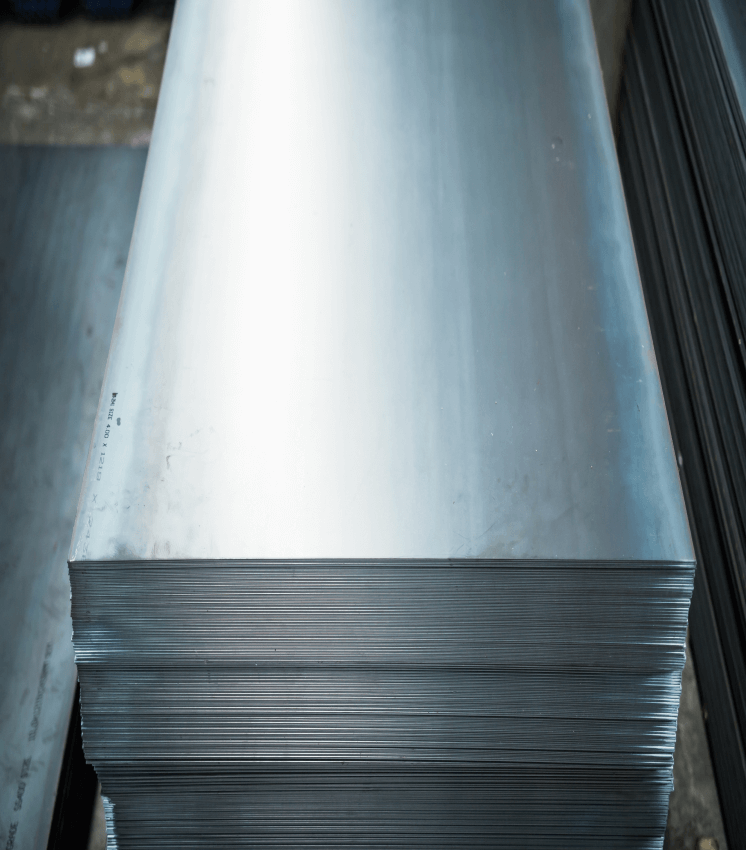
- Automotive: Preheating is used in the automotive industry for processes like forging engine components, welding frames, or preparing parts for coating and painting.
- Aerospace Industry: Aerospace components, often made from high-performance alloys or composites, are preheated to ensure material integrity during forging, molding, or assembly processes.
- Metalworking and Foundries: In metalworking, preheating is used before forging, casting, or extrusion to enhance material flow and reduce the risk of defects. Foundries often preheat molds to prevent thermal shock and improve casting quality.
- Electronics Manufacturing: Preheating is used before soldering or encapsulating electronic components to ensure proper adhesion and prevent damage from thermal shock.
- Construction: Preheating is employed in the construction industry for processes like welding steel structures, preparing surfaces for coating, or curing concrete in cold environments.
- Textile Industry: In textile manufacturing, preheating is used to remove moisture from fabrics before dyeing or laminating, ensuring uniform color and adhesion.
Ready to Optimize Your Manufacturing Process?
At Horizon, we're not just building industrial ovens; we're creating solutions that drive your business forward in a cost-saving, eco-friendly way.Contact us today to discuss your needs and discover how a custom Horizon Oven with Cyclone Technology™ can revolutionize your manufacturing process!